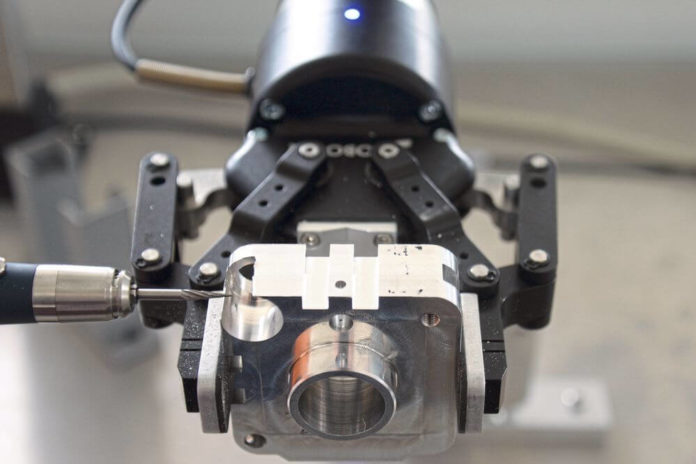
The new Eneska-robotics premiered at Moulding Expo 2019. The cobot is a new solution from joke Technology for automating production.
joke Technology has developed an intelligent robot for deburring, grinding and light polishing work, which was presented to the audience at the Moulding Expo. It is not a device, but a complete concept that derives the work steps and the appropriate design from the desired result. The result is a Cobot (collaborative robot) that is easy to train and takes over the monotonous, ergonomic or health-critical work steps.
Many production processes require a surface finish. If the number of these workpieces to be deburred, ground or polished increases, there can be several consequences. On the one hand, users must always repeat the same movements, which is ergonomically disadvantageous. The health risk is increasing, especially when processing materials that release dust which is hazardous to health. After all, it is becoming increasingly difficult to find qualified personnel for these demanding production steps, especially if they are only necessary occasionally or, on the contrary, if they resemble routine assembly line activities.
In addition, the quality of human post-processing can vary or even decline in the course of production. The Eneska-robotics offers a reliable and reproducible solution for this, which ultimately allows more attention to detail to be put into the finishing process.
Cobot with 6 axes and 5 tools
Eneska-robotics was completely designed and developed by joke. The basic system at Moulding Expo is a six-axis robot with five different drives for different work steps (grinding, polishing or deburring). These can be linear, rotating, for internal or external surfaces, with brushes, files or milling. Eneska-micro control units are used here as the drive. The robot can either guide the tool or the workpiece – both are possible. The great advantage of a Cobot is that it supports the user and works together with him. Protective devices are not generally necessary, since the robot automatically switches itself off when it touches the human being.
Simple teach-in, also via CAD or reference points
The training of the Cobot, which movements he should execute, can be done by the customer himself or the experts of joke. Besides the guided movements there is also the possibility to read CAD drawings or to define reference points. The device can be extended with a camera system and can thus be used for new and additional processing steps.
Just like these, each Eneska-robotics has its own concept: “This gives our customers the opportunity to delegate the unpleasant or hazardous work steps to the machine,” explains project manager Jürgen Meyer. “We have always asked the question in discussions with customers: What can a robot do for you? Dirty or monotonous work, that would be great, was usually the answer.”
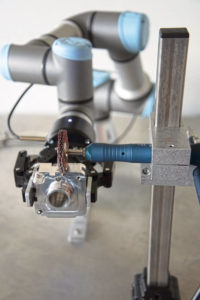
Robot support as a solution for staff shortage
In deburring and machining, there is generally little offspring and, due to the ergonomically demanding activities, a fairly high illness rate. “These tasks are often tiring or harmful to health,” explains joke managing director Udo Fielenbach. At the same time, demand is growing due to the introduction of additive manufacturing. Many companies are accordingly confronted with personnel bottlenecks. “With Eneska-robotics, we are giving companies, for example in the field of implants, the opportunity to employ their experts for important work and decisive quality tests,” says Fielenbach, outlining the vision. “The future of surface treatment is collaborative!”
Technical Details & Equipment
Eneska-robotics is available in various versions. Depending on the application and the materials to be processed, joke creates an individual concept and supports the integration into the company or the production processes.
- Load capacity 3 – 10 kg
- Range 500 – 1300 mm
- 6 joints of 360 degrees each, accuracy of +/- 0.1 mm
The Eneska-robotics is 100% “made in Germany” and will be available at the end of 2019.