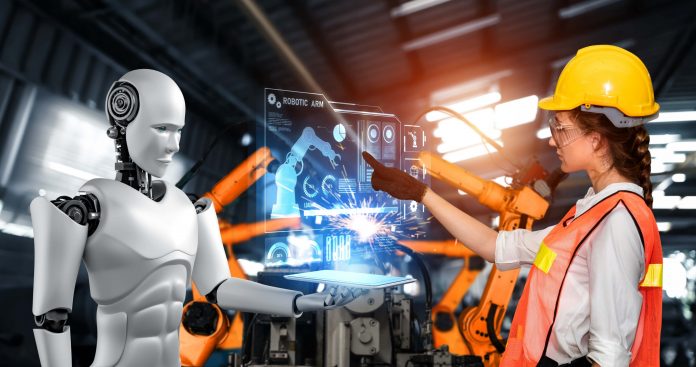
Robotics and robots have been among us for quite some time and are used to separate humans from dull, automated, dangerous or dirty jobs and tasks in warehouses and factories. Safety is probably one of the most important factors when talking about replacing humans with robots.
Robots injuring or even worse, killing their human colleagues, is become even bigger issue as automation rises and many more factories are adapting automation.
In 2016, Forbes published the story about the incident where a semi-autonomous driving Tesla car collided with a tractor-trailer in Florida, killing its driver.
But it also highlights lesser-known examples, such as when an industrial robot killed a German factory employee in 2015 and another killed a Michigan worker in 2017.
In The Future of Jobs Report, more than 80% of business executives said they are accelerating plans to digitize work processes and deploy new technologies. 50% of employers are expecting to accelerate the automation of some roles in their companies.
Who takes the blame?
Robots can’t be blamed for the accidents they cause, of course. Accidents must be attributed to the people behind the machines—to human error, miscalculations or programming errors. That’s why initiatives are needed to prepare the workforce for automation and to operate robots both effectively and safely.
How to prevent accidents?
When company decides to introduce automation to its factory, reskilling employees is the key and most important task which must be done immediately.
Workforce transitions in a time of automation, estimates that as many as 375 million workers—or roughly 14 percent of the global workforce—may need to reskill in digitization, automation and artificial intelligence by 2030, says the McKinsey Global Institute report, “Jobs lost, jobs gained”.
Adapting workers to automation often identifies with large-scale shift from agricultural work to manufacturing in North America and Europe, during the early 20th century.
Digital skills and qualifications
Making sure workers have the right skills to deal with robots, and automation in general, won’t be easy, and different companies are approaching this in different ways.
Upskilling workers seems to be the most popular course—one example is Amazon’s ‘Upskilling 2025’ initiative, an announcement that it plans to spend $700 million dollars to retrain a third of its workforce with skills for automation.
Other companies have further to go. 52% of industrial workers interviewed in the Digital Factories 2020: Shaping the future of manufacturing report by PricewaterhouseCoopers (PwC) believed their company lacks a true digital culture.
Automation will create, as well as reduce, opportunities for employees of varying skill levels. It will require higher levels of skill from some workers, while reducing the levels of skill needed from others.
Therefore, companies must invest in and train their staff to get the most from the latest human machine interfaces (HMIs) for robots, along with SCADA and enterprise resource planning systems—wherever they fall on the skills ladder.
The PwC report says:
“It is absolutely vital to include employees at all stages of developing and introducing new technologies”
The report suggests that workers be involved in evaluating possible robotic technologies. That includes testing and rolling out the technologies in pilot projects; and finally rolling them out in production.
Staff training is the key to safety
Getting workers involved, and trained, with technologies at the earliest stages can double-up with effective risk assessment and understanding potential safety hazards.
Safety and training can go hand-in-hand by ensuring each worker is trained to follow the safety protocol and avoid risks of on-site accidents and injuries—whatever their skill level.
Training of the safe use of robots also goes beyond the technologies’ installation. As the national safety guidelines for the manufacturing industry are always changing, periodic training must be delivered to workers to ensure they can operate the machinery safely.
Safety of robots
The safety of robots must also be guaranteed over the long-term. One way to achieve this is being explored by MIT in collaboration with the automobile manufacturer BMW.
By using simulations to develop algorithms that help robots predict and respond to humans in close proximity, such as on a car production line.
Furthermore, effective maintenance is absolutely crucial to the safe operation of robots.