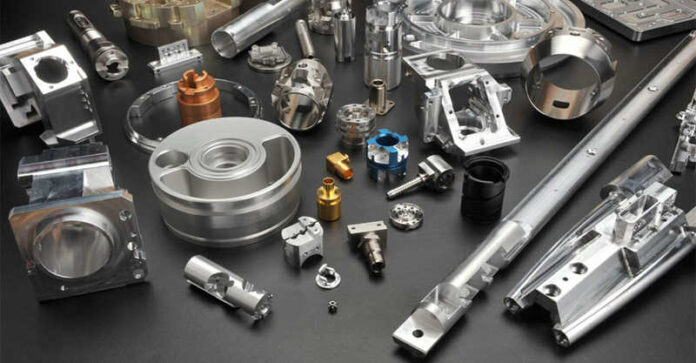
CNC Machining is a manufacturing process in which a set of pre-defined computer codes are used to manipulate how the existing machinery such as lathe, grinder, milling machine, would behave. These codes are generated with the help of CAM software that converts CAD drawing of parts into a series of specific codes that control every aspect of the machining process. From feed rate to tool distance, CNC machining requires almost no human input in order to operated and CNC parts are in many ways better than traditionally manufactured products because failure in any critical component could lead to disastrous consequences. Types of CNC Machining Processes
To put it simply, CNC machines are the same as a traditional machine, but it comes with the added benefit of computer control and sometimes along with multi–axis capabilities. Depending on the operations required, different types of CNC machines are used in the industry. For example, a CNC Lathe can perform machining operations involving cuts in the circular direction and unlike manual lathes; a CNC lathe can also be used for creating complex geometries. Similarly, other CNC machines and as CNC Mill, Water Jet Cutter, Plasma Cutter, and others allow users to perform additional processes that would either be too complex or impossible for a manual machine.
Why CNC Part Machining is becoming Popular Globally?
For any manufacturing plant, opting for CNC Machining instead of traditional machining has become an obvious choice due to its numerous advantages. CNC parts have better tolerances overall and their repeatability is off the charts. This is due to the fact that the performance of a human operator may get affected due to several external factors and the operator’s precision would drop with time, however, CNC can operate with the same precision throughout the day and can also prepare more parts in the same timeframe. With a CNC machining, rapid prototyping gets extremely easier and your plant can be operated without a break. Similarly, with CNC parts, the acceptable tolerances of machined products have reduced a lot because modern machines can provide tolerances up to the factor of 10-3. For high-intensity applications in sectors like aerospace and defense, this is quite important.
Major Applications of CNC Parts
Whether it’s an industrial product or a prototype, CNC parts have a wide range of applications in every sector. CNC parts are quite popular in industries such as aerospace because of their precision and the ability to create extremely complex geometries with relative ease. The most commonly used material in the aerospace industry is Aluminium due to its excellent mechanical properties. Special techniques are required to make CNC aluminium parts and at Wayken, our comprehensive understanding of these techniques and our state of the art facility make us one of the leaders in the market.
In addition to that, CNC Parts are also integral for the metal fabrication industry, there are various operations being performed on metal sheets with extreme accuracy. As the world is leaning towards Nanotechnology, the demand for more precise and accurate machining has also increased, and with CNC technology, these requirements can be fulfilled.
Problems Associated with CNC Aluminium Machining
Although CNC Parts are far better due to an accurate machining process, CNC aluminium parts pose a problem during the manufacturing process. The most prominent problem faced during CNC machining of Aluminium parts is overheating, which cases the part to deform and sometimes melt. This happens because not all Aluminium alloys are suitable for machining, also selecting an appropriate feed rate and tool is extremely important for creating CNC aluminium parts. Only an experienced CNC operator can work on aluminium parts and select appropriate cutting parameters in order to ensure the best results. At Wayken, all our employees are trained to create custom machined parts according to your needs. In addition to selecting the appropriate parameters, there are several other techniques that can improve the results, some of them are as follows:
Symmetrical Machining
With this technique, heat is distributed more evenly across the work piece resulting in better heat dissipation. With this technique, we can avoid heat concentration on the part which would ultimately reduce deformation of the machined part.
Stratified Machining
In this method, cavities in the work piece are dealt with at the same time, making it harder for the uneven forces to deform the part. With the application of uniform force, stress concentrations in the part will be reduced which would increase the lifecycle of the part.
Optimization of the Cutting Tools
It is obvious that the properties of the cutting tool would play an important role in the machining process. The combination of the geometric and material properties of the cutting tool allows us to control the applied force and heat dissipation on the part. By changing the front angle, rear angle, helix angle and the main deflection angle, we can change the force applied on the part and the average temperature of the processing area.
Strictly controlling tool wear
As described above, the cutting tool is quite important for the machining process, so it must be properly cared for. With regular inspection of the cutting tool and proper maintenance, the results can be significantly improved.
Selecting the best alloy
Not all alloys of Aluminium are suited for precision machining process, though their performance can be increased by applying the above-mentioned techniques, it is better to select an alloy with mechanical properties suited for this process. Aluminium grades such as 6061, 7075, 2024, 5052, and 6063 are some of the popular choices for CNC aluminium parts.
Source: geospatialworld.net