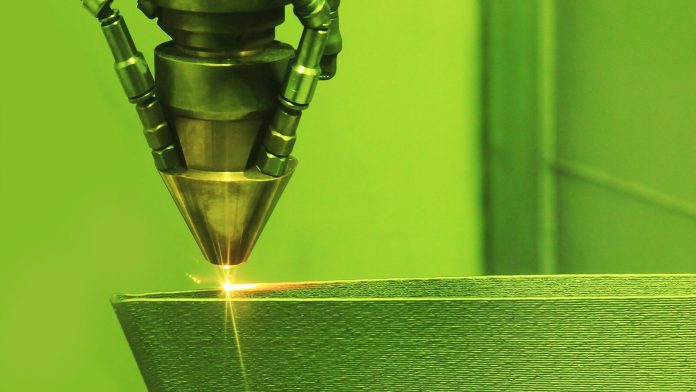
A team of researchers from Argonne National Laboratory and Texas A&M University have developed an innovative new approach to defect detection in 3D printed parts.
Using real-time temperature data, together with machine learning algorithms, the scientists were able to make correlative links between thermal history and the formation of subsurface defects during the laser powder bed fusion process.
Aaron Greco, a co-author of the study, explains: “Ultimately you would be able to print something and collect temperature data at the source and you could see if there were some abnormalities, and then fix them or start over. That’s the big-picture goal.”
Porosities in 3D printed parts
As sophisticated as 3D printing is, even the higher-end industrial systems struggle with porosities – voids in the 3D printed part where metal powder has not fused sufficiently. These porosities often result in ‘weak spots’, making components prone to cracking and fractures.
There are a number of different reasons for porosities to form, including inconsistent powders and insufficient laser strengths. According to Noah Paulson, lead author of the paper, the Argonne work showed that there is a distinct correlation between the surface temperature of a part and the porosity formation inside.
Machine learning and powder bed fusion
To facilitate the research, the scientists made use of the high-powered X-rays at Argonne’s Advanced Photon Source (APS), a Department of Energy facility. The team designed and built an experimental PBF rig with in-situ infrared cameras, which would go on to 3D print parts made of Ti-64 powder.
During printing, the camera was used to capture temperature data while the X-ray beam was used to view the printing process from the side, giving an indication as to whether or not porosities were being formed.
Paulson adds: “Having the top and side views at the same time is really powerful. With the side view, which is what is truly unique here with the APS setup, we could see that under certain processing conditions based on different time and temperature combinations porosity forms as the laser passes over.”

Source: Argonne National Lab
Interestingly, when comparing the thermal histories to their respective porosity profiles, the scientists found that low peak temperatures followed by gradual decreases were likely to be correlated with few porosities.
On the other hand, high peak temperatures followed by dips and subsequent increases were likely to result in more porosities. Using their data sets, Paulson’s team then went on to build machine learning algorithms that could accurately predict porosity formations just based on the thermal histories recorded during the printing process.
The ability to identify where porosities are likely to form just from infrared imaging is a very powerful tool. It eliminates the need for costly individual part inspections, which are not always feasible when dealing with high production volumes. Paulson’s research team is hopeful that the work can be developed and improved with more data sets and a more sophisticated machine learning model in the coming months.
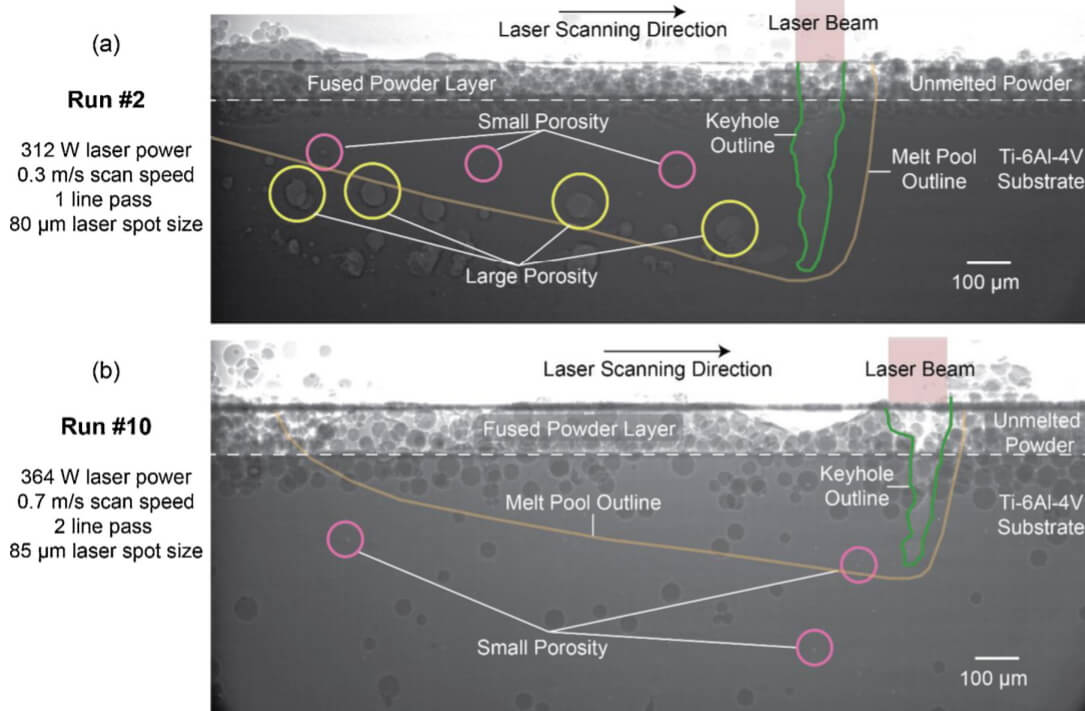
Source: Argonne National Lab
Further details of the study can be found in the paper titled ‘Correlations between thermal history and keyhole porosity in laser powder bed fusion’. It is co-authored by Noah H. Paulson, Benjamin Gould, Sarah J. Wolff, Marius Stan, and Aaron C. Greco.
The predictive power of machine learning is really starting to be utilized in many aspects of additive manufacturing. Researchers from New York University recently used machine learning algorithms to reverse engineer glass and carbon fiber 3D printed components. By feeding CT scans of 3D printed parts into their models, the scientists were able to “steal” the toolpaths used to manufacture the parts, all while maintaining the intricacies that give them their strengths and durabilities.
Elsewhere, at the Swinburne University of Technology, a researcher has used machine learning to give insight into the compressive strength of 3D printed construction materials. With the aim of developing a process for classifying different 3D printed geopolymer samples, the researcher targeted specific variables, and optimized the makeup of the 3D printed materials using machine learning models.