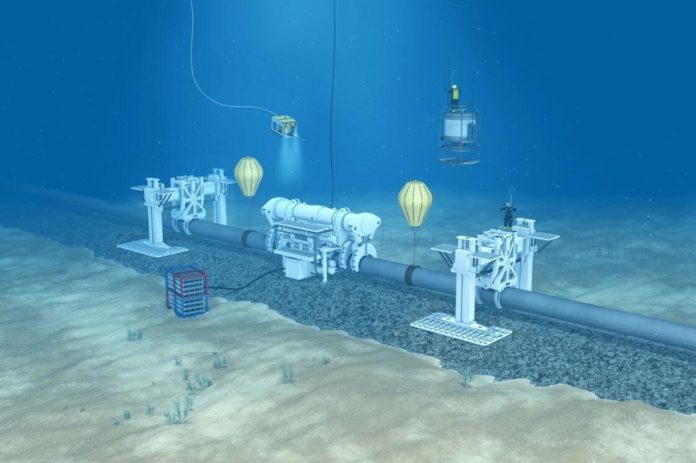
The 1,166 km Langeled Pipeline has helped Norway and Britain to scale new heights with regard to their oil and gas export and import business.
Part of the Ormen Lange gas field, the Langeled Pipeline will transport about 20% of the UK’s gas demand. This pipeline is an amazing display of engineering skill and the determination of the human mind. A massive budget of 1.7 billion pounds, and a record construction period of three years made this engineering wonder a possibility.
Today, the Norway and British oil and gas exploration industry are reaping the fruits sown by three oil and gas exploration giants, namely ExxonMobil, Stat Oil, and Royal Dutch Shell.
The Langeled Pipeline
Langeled is the world’s longest underwater pipeline. It transports Norwegian natural gas through the North Sea from Nyhamna Terminal, part of Ormen Lange field in Norway, to the Easington Gas Terminal in England. Along this journey, the pipeline goes through a connector at Sleipner Riser where natural gas can also be transported to continental Europe.
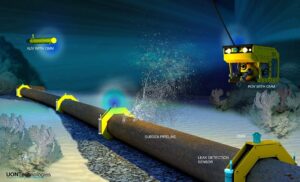
Discovered by Hydro in 1997, Ormen Lange is the second-biggest gas field offshore in Norway. (The largest offshore gas field in Norway is Troll.) The name comes from Norse mythology where it refers to a giant serpent that encircled the Viking world. The modern version of Ormen Lange refers to natural gas reserves of 397 billion cubic meters held in seabed wells at depths of 800 to 1,000 meters below the water surface… and the pipeline used to transport the gas stream from the production platforms to a processing plant at Nyhamna.
Engineering the Langeled Pipeline
Before any pipe was installed, engineers had to successfully plan the project to overcome the unique challenges of the North Sea. For example, the seabed needed to be surveyed. An underwater vehicle called the Hugin was used to give the project design engineers an understanding of the surface the pipeline would have to travel across. The Hugin was supplied by Kongsberg Maritime and the Norwegian Underwater Institute and traveled in depths as much as 4.5 km.
The pipeline was laid across a treacherous seabed. A remote-controlled excavator, the Nexan Spider, was used to prepare the seabed so that the pipeline could traverse steep slopes and uneven terrain. Rocks that were in excess of 60 m high were removed by the excavators. In addition, 2.8 million tons of rock was lowered to the sea floor to level out some of the terrain.
The steel pipeline is 42 inches in diameter along the northern section from Nyhamna to Sleipner Riser, and 44 inches in diameter along the southern section to Easington. In total, 96,600 pipe sections were laid. Two large pipe laying ships, the LB200 and the Soltaire, which is the largest pipe-laying ship in the world, had the task of laying 4 km of pipe per day. After the pipe was laid, divers had to make sure that it was prepared for welding. They did this in a watertight construction area called the Pipeline Repair Habitat where they could make any repairs that were necessary. Hyperbaric welds, a type of underwater welding, were used to join the sections.
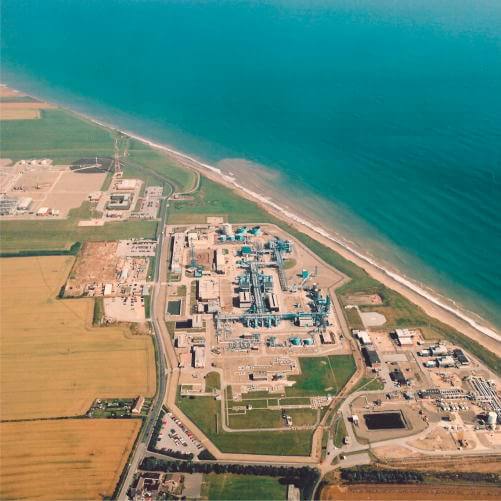
Source: BBC
The submerged pipeline had its share of environmental complications, but integration of Environmental Impact Assessments (EIA) with the engineering developments, time, and resources enabled the working parties to keep a check on the environmental impacts of constructing the pipeline and formulating possible risk mitigation solutions.
The Easington gas terminal of the pipeline in England. The owner of the terminal is British Petroleum, and the overall floor area of this terminal is 87.5 acres. The Dimlington site serves as the controlling and conditioning site.
The Langeled Pipeline is able to carry 25.5 billion cubic meters per year of North Sea gas. Approximately 3,000 workers participated in the construction and contributed to the successful opening of the southern section in October 2006. Hydro was the operator of the pipeline in the development and construction phase. Now the pipeline is owned by Gasled and operated by Gassco.
The total cost of the project was £1.7 billion, and its development made Norway the second largest exporter of natural gas after Russia. The best thing about this project was its completion within time and that too without comprising a bit with the safety aspects.
The safety achievement on the Langeled Project was the best ever among Statoil’s pipeline projects.