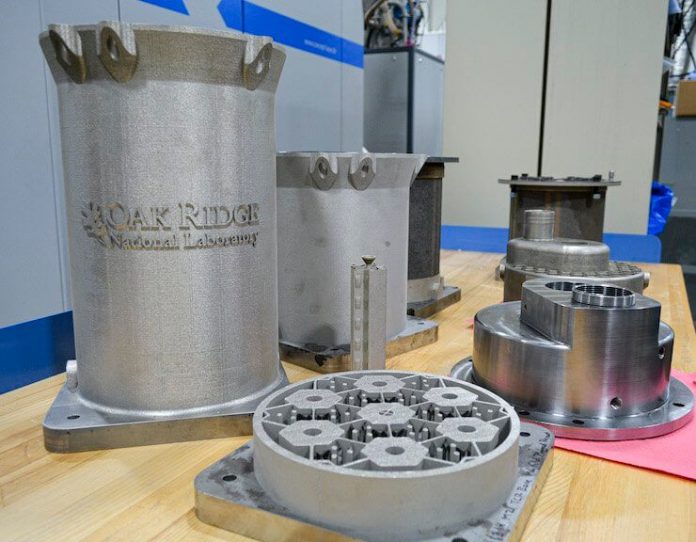
Oak Ridge National Laboratory (ORNL) is working on the design of a 3D printed nuclear reactor core which is scheduled to be turned on by 2023.
Researchers at ORNL are currently refining the design, while also working to scale up the additive manufacturing process to build it and develop methods to ensure the consistency and reliability of additively manufactured components.
Assessing that nuclear reactors are designed and manufactured based on decades-old methods, which in turn bring higher costs and longer lead times, the US Department of Energy (DOE) has deployed ORNL researchers to harness the advances in manufacturing, materials, nuclear science, computing and data analytics to develop a modern nuclear reactor design.
ORNL’s Transformational Challenge Reactor Demonstration Program (TCR) has completed a three-month ‘sprint’ which demonstrated additive manufacturing’s proficiencies in rapidly prototyping the reactor core and is also planning to set up a digital platform that will help in ‘handing off’ the technology to industry for the ‘rapid adoption’ of the additively manufactured nuclear energy technology.
The programme has been set up in a bid to address the United States’ looming shortage of nuclear reactors. Around 20% of US electricity is provided by nuclear power plants, but more than half of the country’s reactors are to be retired within 20 years (based on current license expiration dates), while only one new nuclear power plant has been built in the last 20 years, largely due to the decades-long lead times associated with their construction.
“The nuclear industry is still constrained in thinking about the way we design, build and deploy nuclear energy technology,” commented ORNL Director Thomas Zacharia. “DOE launched this programme to seek as new approach to rapidly and economically develop transformational energy solutions that deliver reliable, clean energy.”
“We have been aggressively developing the capability to make this programme a reality over the last several months, and our effort has proven that this technology is ready to demonstrate a 3D printed nuclear reactor core,” added Kurt Terrani, the TCR Technical Director. “The current situation for nuclear is dire. This is a foundational effort that can open the floodgates to rapid innovation for the nuclear community.
“The entire TCR concept is made possible because of the significant advances in additive manufacturing process technology. By using 3D printing, we can use technology and materials that the nuclear community has been unable to capitalise on in the last several decades. This includes sensors for near autonomous control and a library of data and a new and accelerated approach to qualification that will benefit the entire nuclear community.”