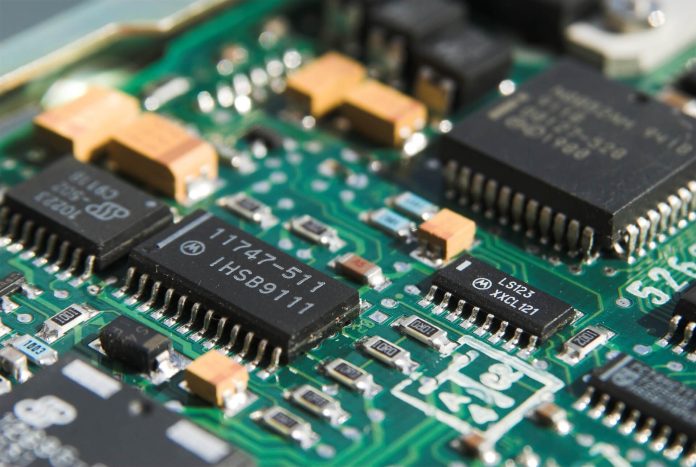
Additive manufacturing, also known as 3D printing, is changing the way electronics engineers perform their jobs, offering new ways to produce, test, and design products.
There are two methods in additive manufacturing within electronics: inkjet-style printing and 3D circuit board manufacturing. Inkjet printing works on two dimensions across printed circuit boards (PCB). The method typically uses a printhead on a level surface that applies a conducive aerosol deposition onto the PCB.
The method delivers high resolution and a consistent finish. Inkjet printing offers accuracy when applying a design while reducing the number of steps in the manufacturing process. This style of printing suits the rapid production of custom PCBs.
As for 3D circuit board manufacturing, the process involves an extruder header applying droplets of conductive metal on the PCB. The method allows for free-flowing wires that connect within the two-dimensional PCB. Materials will add up, layer by layer, and the coupling prevents the board from constraining the circuits. These connections have been borderline impossible given modern circuit board technology.
Additionally, 3D circuit board manufacturing only uses materials that are essential to production. The increase in efficiency and the ability to transform 2D and 3D circuit combinations have made additive manufacturing a prescient technology in the electronics industry.
The 2D approach typically has a printhead that releases conductive ink onto the PCB. It may also extrude two chemicals that react on the board to create a small bead. The 3D method is more complex and uses extrusion and material methods, which can include:
- Conductive aerogel
- Conductive gels
- Embedded copper-conducting filament
- Graphene substrate printing
The application of 3D printing serves manufacturers of all sizes. There is a specific niche for it within large-scale production of PCBs. This application will likely yield advances in electronic additives.
In addition, the technology can bring circuit board production to the household or individual level for DIY creators or startup companies. Additive manufacturing would allow users to create a prototype for a circuit board without the investment or risk of touching harsh chemicals that PCB manufacturing requires at a large scale.
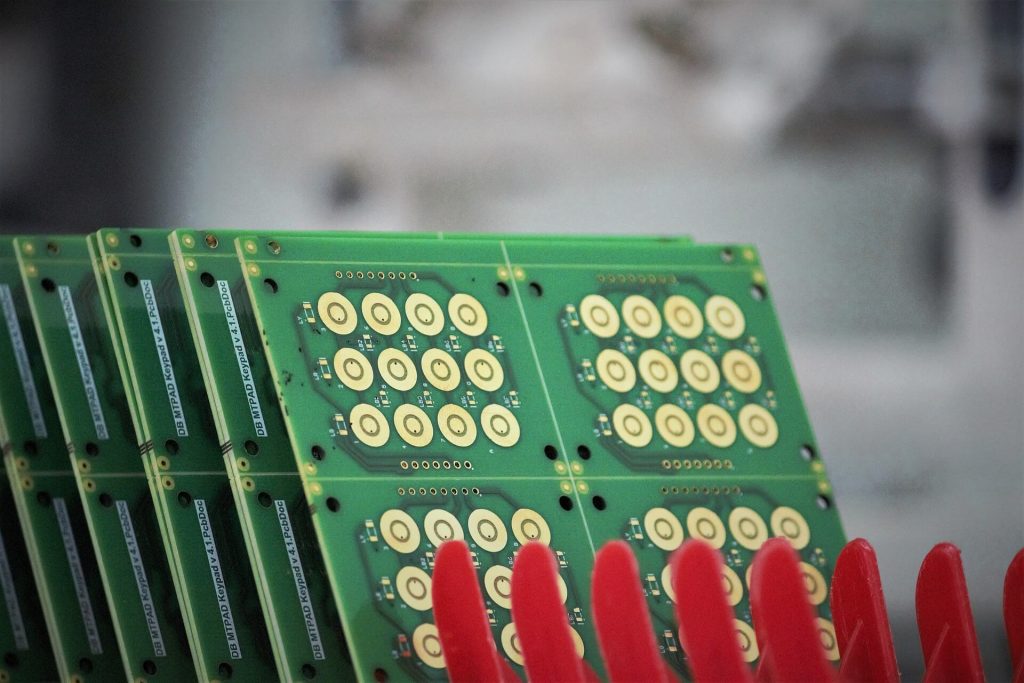
Complementary Functions
Additive manufacturing does not have to replace the existing methods. Currently, it is playing an integral role that has spurred scientific and engineering advances. At minimum, additive manufacturing will transform the way companies handle electronics production.
Several aerospace and automotive companies are using additive manufacturing to develop tools and fixtures rather than use subtractive manufacturing processes or injection molding as it saves weeks of time.
The same functionality applies to sensors with integrated wireless capabilities. When a 3D printer produces a PCB, there are no limits to the form or geometry. The system will enable functional electronic components, such as integrated battery holders and wireless sensors embedded on the PCB.
New materials and systems in additive manufacturing
Currently, additive manufacturing has many materials, though they are relatively specialized. For instance, some are specialized for specific deposition applications, like inkjet printing or fused deposition molding. Many systems also do not have the versatility to handle diverse materials, which is problematic when manufacturers want to scale production.
Additive manufacturing and electronics are opening doors to new opportunities and innovations. Designers and engineers can rapidly create and print prototypes in a way that was not feasible years ago. The effects have the potential for sweeping improvements across industry, too, for everything from medicine to material science.