
With flexible modern CNC production equipment, any enhancement of tools and innovations that are brought to market can be easily integrated. Avoiding large reconstruction that requires huge capital expenditures and shooting equipment to install new equipment can save big money producers.
Drilling holes play a key role in car manufacturing. Hundreds of holes must be drilled for each manufactured vehicle, including those in the transmission shafts, engine blocks, air suspension paddles, camshafts and other internal parts of the engine. In any production line of parts of automotive parts, the movable straps work without ceasing and effective tools are a key aspect of profitability. Every minute when the spindle does not bore holes or effectively removes scraping by drilling, it is the minute you lose money. Manufacturers need to make use of apparently small changes in the tools because they can make a big difference in the efficiency of the holes. Innovative technology is now available that can be integrated directly into the process without closing production. Adopting these innovations that reduce costs can significantly increase the company’s margin.
Installation of tools in automotive production
In the past, all major cutting and drilling machines were equipped with portable lines on dedicated machines. These machines set high-speed rotation speeds that transmitted parts between the processing station, where they waited for the operation to take place. The default number of parts can be punched in one day; Moreover, if one machine is broken, the whole line is gone. There was no advantage in developing cutting or drilling tools that accelerated the work because the line could only work at a certain speed.
This outdated approach to automotive production continued during the 1970s and 1980s, but slowly began to change in the nineties of the last century with the development of computer numerical devices (CNCs). Today’s modern car makers now use flexible CNC equipment; If parts can go faster on one machine, they can accelerate to the next, perhaps gaining advantage that ultimately turns to higher revenue. With these new CNC transmission lines, manufacturers can be more flexible, making changes and exploiting all new tools that come out. They can take advantage of innovation tools that help them increase production and earn more money. Those in the tool industry are therefore always looking for new and innovative tools that can accelerate the slowest part – one that retains other operations – which can bring significant total cost savings.
Industrial trends affecting metal cutting in the automotive industry
One of the main factors affecting metal cutting in the last 20-30 years is the long-term removal of free metal machineries, those that can be easily cut, allowing the removal of materials with a satisfactory finish at low cost and without the need for tools to be worn. By removing lead in metals and replacing cast iron with compact graphite iron (CGI), the metals used in the automotive industry have shifted from machine-to-machine to extremely hard-to-machine. This means that the tools have to be adjusted to increase the chip control to achieve tool life and make the hole flat. Other changes in the industry that impact hole drilling holes are environmental laws that restrict the use of chlorine and sulfur in cooling well systems. (The scope of this problem is different in Europe, which requires dry processing, which does not use any refrigerant, or very little, because the removal of refrigerant is prohibited by the polluting laws.) Elimination of chlorine and sulfur resulted in increased chip building problems cutting tool, chamfering, and reduced tool life.
The end result is that tool manufacturers must find innovative ways to address these trends. Tool manufacturers had to innovate to improve the performance of their tools. Some companies are moving near network grinding to avoid these problems, but the problems will continue, as parts will always differ from counterfeiters to counterfeiters.
Innovative tools make older machines work as new
In response to these automotive, economic and ecological / regulatory trends, the market seeks innovation in the flow and drilling – and machinery and tools. In fact, this innovation is what earns money to car makers.
For example, new scraping and drilling machines come into the market with the change of high speed tools and the more accurate spindles of HSK (hollow cone handle) tools. But there are many design tools available that can compensate for the disadvantages of older machines. Placing a 21st Century tool on 20th century machines can significantly improve production efficiency and increase profitability, leading to older machines operating as brand new. Improving existing capital assets can be a big advantage as capital requirements for the purchase of large new equipment can be difficult to finance. With the flexibility of new CNC machines, new tool enhancements can be integrated without any problems – without turning off the production line for reinstalling tools.
One example is the engineering and design work carried out by Allied Machine & Engineering for the Tier 1 supplier of a high-volume, high-volume steel-alloy car carrier, a poor shredder material. The existing tool used a system of low pressure coolant tools and small cone spindles. A very large and abrasive piece of waste was created, which stuck to the outer dimension of the body of the drill holder, lying on the bottom of the holes. With a poor surface surface of the holes, the tool could only drill 200-400 holes per plate and had a high monthly wastes of about $ 20,000.
Allied has carried out research on the creation of chips in their own laboratories – outside the production line of the manufacturer, and not on their spindle, so it did not produce any breaks in production. The Allied Machine Research Laboratory has facilities for simulation of the machine’s exact conditions and pump pressures, which ensures optimization of the chip removal.
The tool Allied developed was a specially designed T-A® Stealth Drill (because it works so quietly), which allows the tool to be drilled longer, produces real holes and evenly wears. The T-A stealth drill has an adjustable wedge that increases the precision of the tool, increases bearing diameter on the holder, and additional coolant outlet in the solder area of the carbide triple holder holder. This design reduces the gap between the bracket and the blade, but increases the support bracket.
The T-A Stealth drill was used in combination with a newly developed special insert with the name of the Ultra T-A insert, which reduces the built-in edge. The Ultra T-A has enabled the car manufacturer top-of-form waste, improved tool life, reduced spindle load, and smooth blade cutting.
Ultra T-A and Stealth Drill technology has enabled low pressure machines to dramatically improve performance compared with modern high pressure refrigeration machines. It has a very small amount of waste, the shavings fall down on the holders, and all the cutbacks on the inner dimension have been eliminated. The new tool delivers excellent surface finishing, eliminating around $ 240,000 per year in waste and increasing tool life to 280 percent. Each insert can drill about 1200 holes – 3 to 6 times more than the previous tool.
Another example of innovation is the hole drilling application in the airbag paddle chamber. Allied recently worked on an operation that produces 7 million units a year. The company also had problems with the formation of waste; the size of the waste virtually created the pillar within the part, which led to the need to remove a large number of pieces.
Researchers in the Allied Laboratory were investigating the problem to understand the symptoms and then devised a tool specifically for the company’s operation and their material. They have developed a tip that is exactly designed with the proper geometry of waste generation, meaning waste of the optimum size comes out of the hole. Using T-A Stealth Drill technology and custom drill inserts, the customer saves three seconds per piece – 7 million times 3 seconds saves a lot of time – and a lot of money.
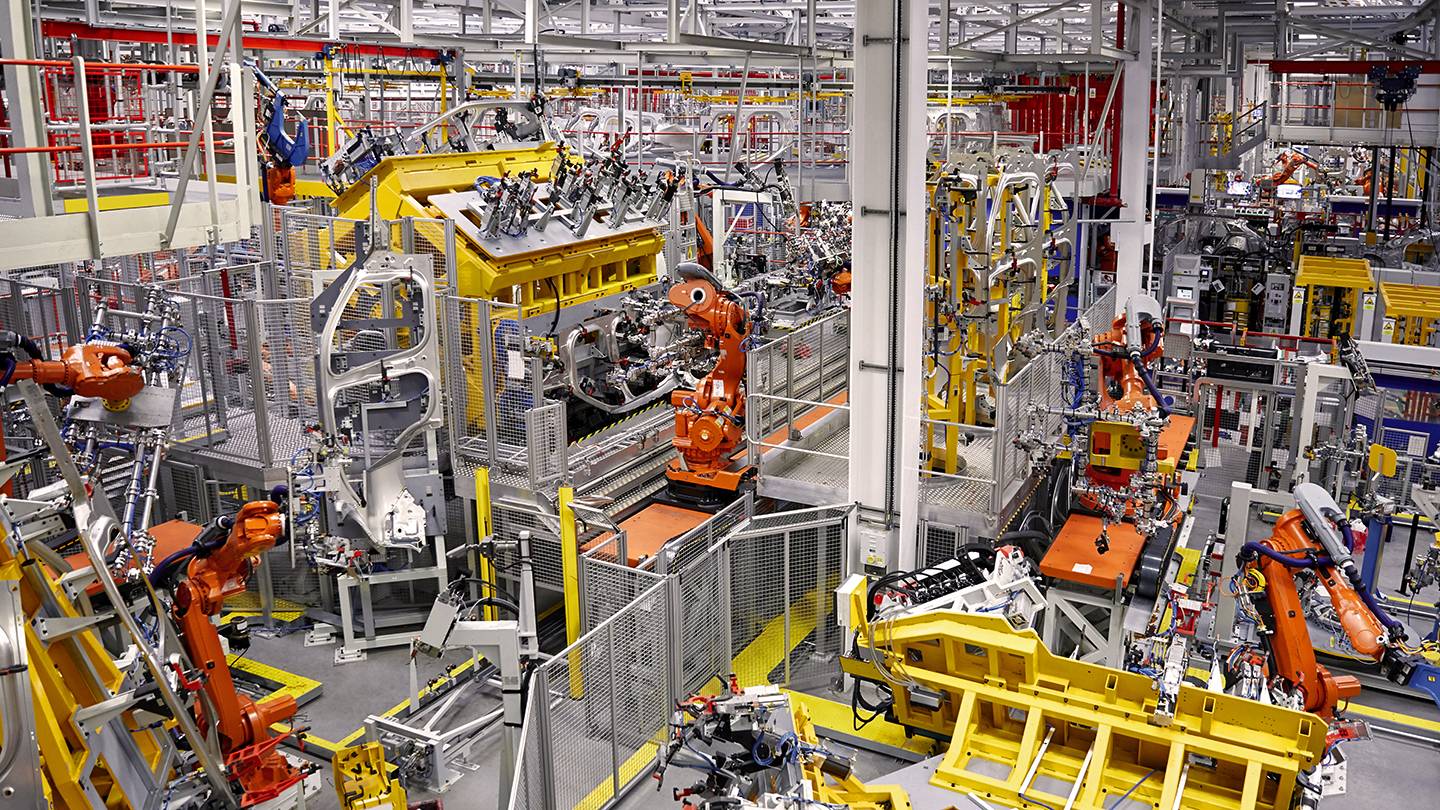
Innovative tools have since been used in various other automotive applications around the world, including a tool designed for the production of crankshafts. The new thread cutting tool and the innovative head for fast changing speeds are newer examples of how the tool can be used to gain the benefits.
With flexible modern CNC production equipment, any enhancement of tools and innovations that are brought to market can be easily integrated. Avoiding large reconstruction that requires huge capital expenditures and scrapping installations to install new equipment can save big money producers and improve their bottom line.