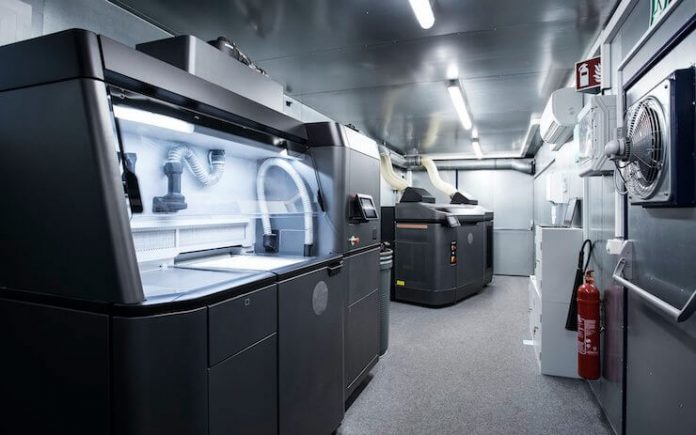
Daimler Buses and its Omniplus service brand have set up a 36m2 mobile 3D printing centre for the decentralised additive manufacture of spare parts.
The mobile container will be in operation at the BusWorld Home service centre in Hamburg but can be transported by truck to any location with only electricity and internet connection require when in operation. This, Daimler Buses believes, will ensure spare parts are delivered to its bus customers more quickly.
Daimler’s mobile container is equipped with a HP Jet Fusion 3D printing system which the company believes is able to meet the production standards for injection moulding and deep drawn parts as stipulated by Daimler AG. The polyamide powder is prepared at a processing station, where the printed part will also be removed from the powder cake after the build, while a blasting system and air compressor are located in an adjacent room. The facility also includes an industrial vacuum cleaner, an air filter and an air conditioning system. Parts can also be painted in a limited range of colours.
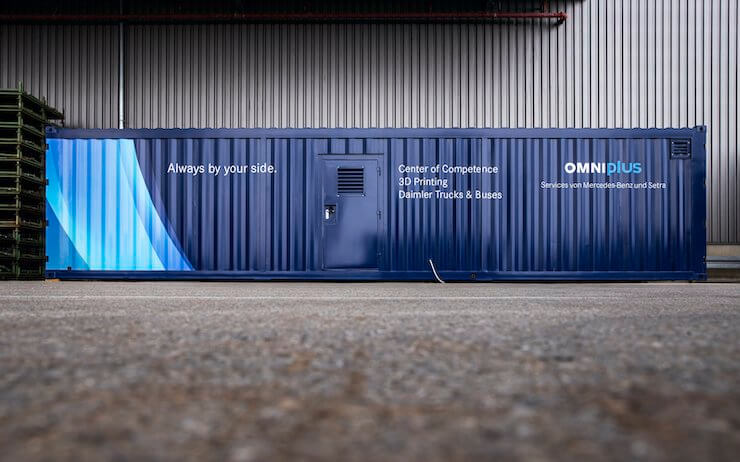
Nearly 40,000 bus spare parts are said to be 3D printable today, with the Daimler Buses team initially focusing on 7,000 components that are currently being digitised. These components will go through approval processes and several product tests before being stored in a digital warehouse with the relevant printing information. Parts will be delivered within a few days, as opposed to lead times of several weeks when manufacturing with traditional processes.
“Thanks to the mobile 3D printing centre, we can exploit the advantages of 3D printing to a greater extent and further increase the speed at which we supply spare parts,” commented Bernd Mack, Head of Customer Services & Parts at Daimler Buses. “Decentralised production of parts as required avoids warehousing costs and reduces transportation routes. Thus, 3D printing not only allows us to react fast, flexibly and economically to customer requirements but to also improve our ecological footprint for the production of spare parts.”
Daimler Buses has also said it intends to further expand and decentralise the business model, with customer able to purchase 3D printing licences from the ‘commerce’ section of the Omniplus On portal and have the corresponding parts produced in a 3D printer centre certified by Daimler Buses.