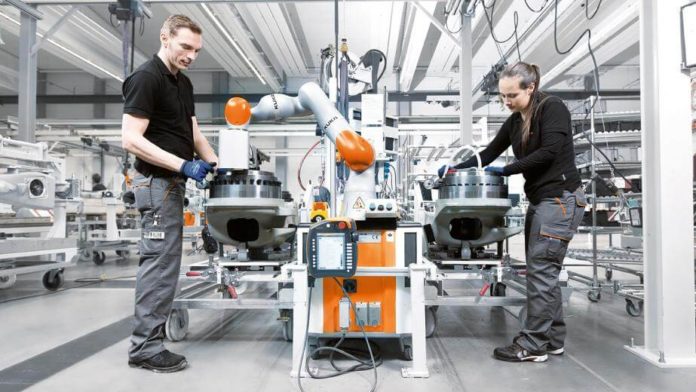
Manufacturers incorporation and adaptation of robotics has developers at work right now, and their innovations likely to influence manufacturing sooner than you expect.
The accelerated pace of automation — and especially robotics equipment — has impacted manufacturing substantially in the past decade, and these developments show no signs of reversing or slowing down. Here are six trends in robotics technology that are underway right now, and are likely to influence manufacturing operations in the near future.
1.Heavy-duty robotic arms
— Heavy-duty robotic arms can keep the workflow moving smoothly and prevent accidental injuries resulting from human fatigue or strain. Market analysts predict the demand for heavy-duty robotic arms will grow to $14.7 billion by 2026, representing a combined annual growth rate (CAGR) of 4.73% for the forecast period beginning in 2017.
Over that time, people who work with robots will see more opportunities to use these types of arms in their workplaces. One example is the Fanuc M-2000 Series robots. The arms on these machines can lift 2.3 tons, and the developer has demonstrated the arms’ strength, reach, and functionality by lifting entire cars as an example for a way to use them.
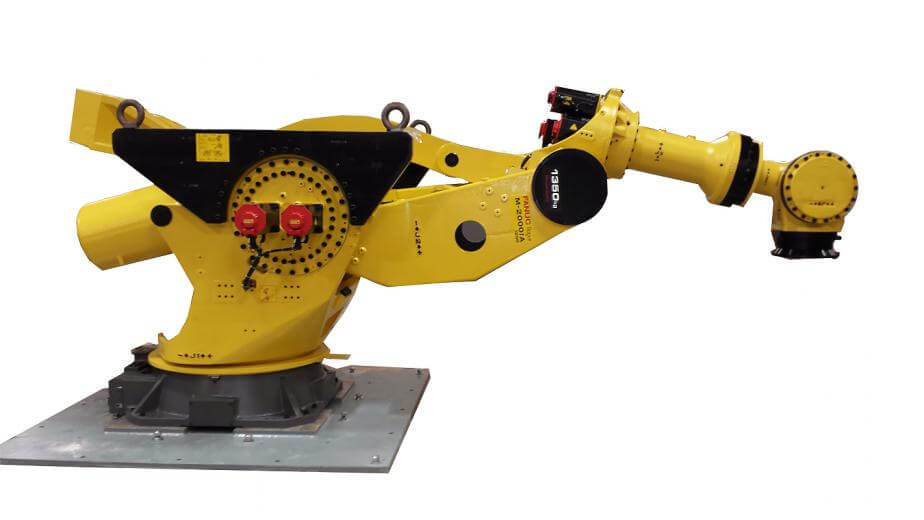
Source: Fanuc
2. More reliance on mobile cobots
— People in manufacturing are accustomed to collaborative robots (“cobots”) that work around or together with humans. There’s a newer trend involving mobile cobots — lightweight and compact enough to move between worksites or areas of factories.
A 2018-2026 market analysis values the global cobot market reaching more than $4.4 million by the end of the period, indicating a CAGR of 33.4%.
A Kverneland Group factory in Denmark produces agricultural machinery and uses a mobile cobot to move pallets of components around the factory. It relies on the robot so much that this model of cobot travels the equivalent of 30 miles in any 24-hour period. The machine is the same size as a pallet, and when fitted with a lifter, it handles more than 1,100 lbs. at a time. Kverneland relied on trucks for internal deliveries, before adopting the mobile cobots. However, due to the constant movement of people around the factory, there were various minor injuries incurred by human workers collisions with those vehicles. The cobots should minimized that problem, significantly.
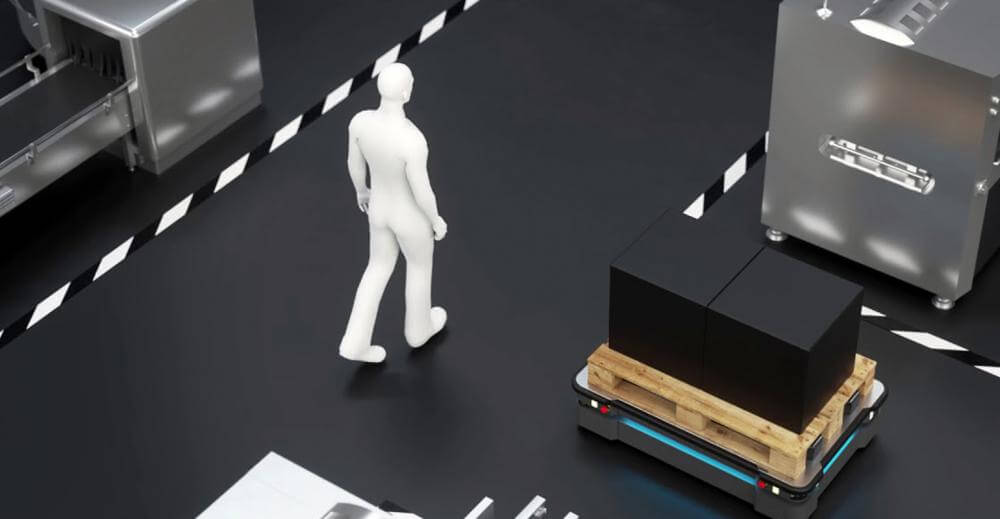
Source: American Machinist
3. Sensors make gigantic robots safer for humans
— Besides the cobots that work safely among people, much larger and more powerful robots typically stay within enclosed workcells, while human workers remain a safe distance away. These arrangements could change over the next five years thanks to efforts intended to make even those massive pieces of equipment safe for humans working nearby.
One company leading the way in this approach is Veo Robotics, a startup that places 3D sensors around the robots so that the machines can use software to build representations of the scenes around them. The software identifies objects and makes estimations about the paths of moving things — including humans. Then, it controls the robots accordingly.
In one test use of the technology, the robots worked around humans at an automotive manufacturing plant and did so safely, even though the robots had 7-foot-long arms.
The CEO of Veo Robotics got the idea for the technology when he visited a different car manufacturing plant and saw people lifting dashboards. Knowing that’s a cumbersome task, he envisioned a day when robots could do that job instead. Depending on how things progress at Veo Robotics, other companies may follow suit with similarly advanced processes.
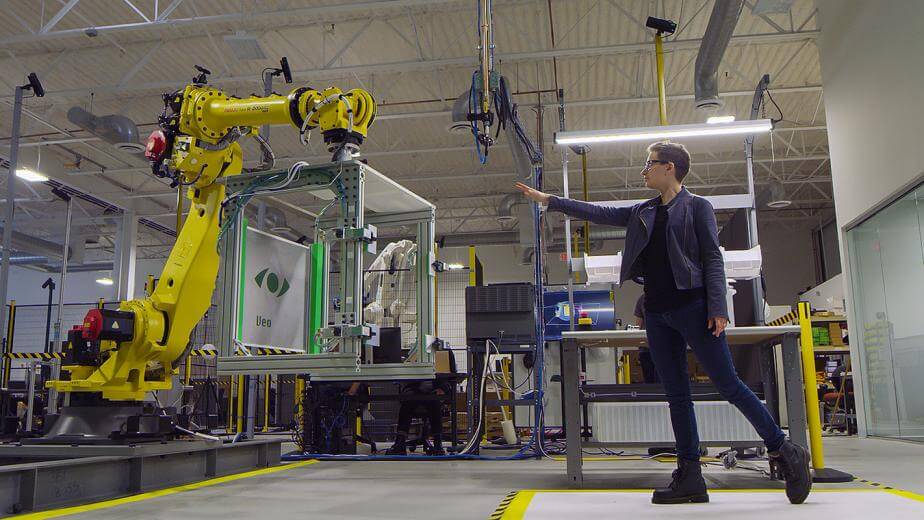
Source: Veo Robotics
4. Toward more hazardous environments
— The growing prominence of robots in various industrial sectors and elsewhere has caused an increased need for robotics engineers. Once those professionals have at least a decade of experience, they often manage the development or creation of new robots, working with their employers to meet different needs that arise.
Robotics engineers deal with perpetual needs, too. One constant need is figuring out how to let robots do the most dangerous work performed by humans.
A poll of workers in the United Kingdom found that at least three-quarters of them want robots to do unhealthy or hazardous jobs. Many people willingly accept work that puts them in harm’s way, and they receive extensive training on how to stay protected — but they know accidents could happen at any time.
Fortunately, robot makers are introducing models that tolerate the toxic gases and strong fumes associated with manual welding, or can work in sections of manufacturing plants that have flammable vapors. Over the next five years, those robots should become more widely used in manufacturing operations, which could leave safer work for humans to do.
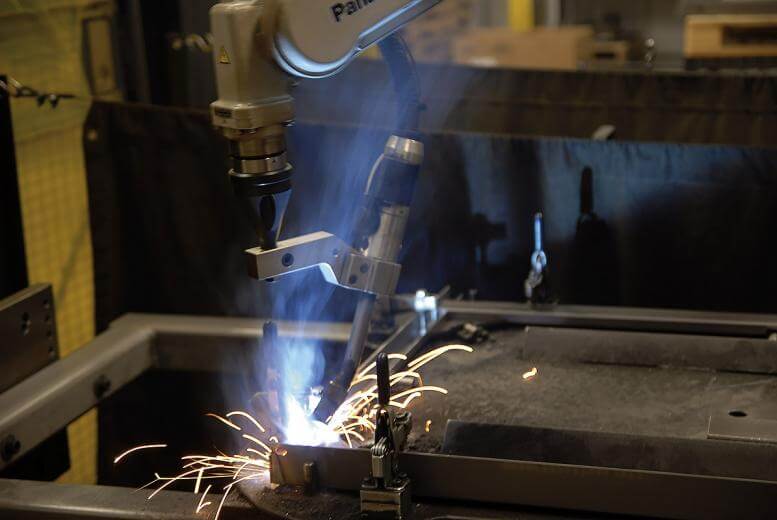
Source: Miller Electric Mfg.
5. Softer robots
— Work is also underway to build robots with softer components. When covered with a material like plastic or rubber that could endure the stress of a robot’s constant movement, such machines would present less danger to humans that come into accidental contact with them. Some of the experiments happening now involve building soft, animal-inspired robots based on things like an elephant’s trunk, caterpillars, or worms.
These are early-stage projects, and notably the progress to date has involved robots that lift only comparatively light loads.
However, there’s one example of a robotic arm that weighs about 1 kilogram and can lift about five times that weight. If scientists figure out how to strike the all-important balance between softness and power, the influence on industrial robotics applications could be consequential.
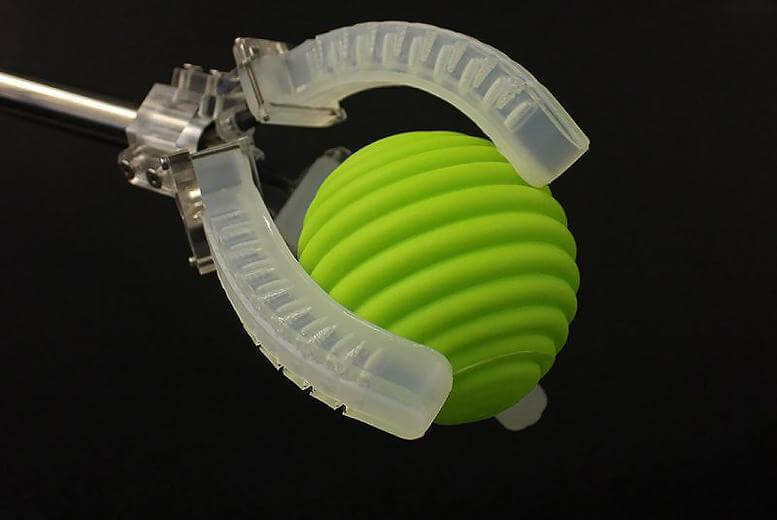
Source: Ryan L. Truby/Harvard University
6. Improved robotic exoskeletons
— Robotic exoskeletons that people wear are not new but many of the previous iterations of the concept limited workers’ movement, because they had to stay connected to power sources.
However, the first battery-powered full-body industrial robotic exoskeleton reportedly will be commercially available in early 2020. The developers claim it will give wearers a 20-to-1 strength amplification. So, to a person wearing this robot and lifting 100 pounds, the load should only feel like 5 pounds.
A market projection shows the global worth of the robotic exoskeleton market reaching $5.2 billion by 2025, and the analysts clarify that these robotic suits are especially helpful for tasks like shipbuilding or airplane manufacturing. In those jobs, people working with heavy components or tools risk serious injury.
The report also suggests that as robotic exoskeletons are tested in more environments and applications, and prove they’re fit for specific purposes, adoption rates will rise speedily and sharply.
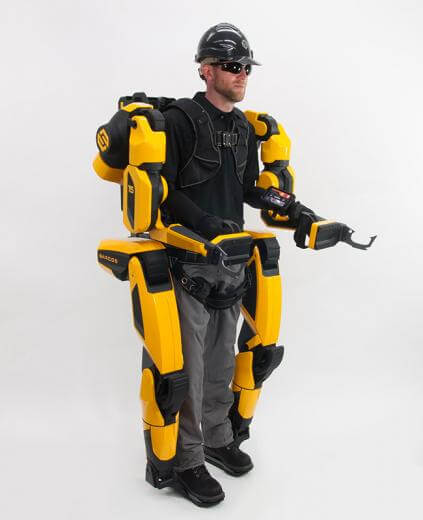
Source: Sarcos Robotics
Assistance for strenuous or dangerous work
Manufacturers already rely on robotics for tasks that demand precision or durability, or risk, and the developments listed here show the variety of ways they may depend even more on robots to take care of repetitive lifting, or jobs involving hazardous conditions.
But, once the operators begin to think more practically about the ways to use these new robotic concepts, and others like them, they are likely to discover entirely new ways to get their manufacturing tasks completed.