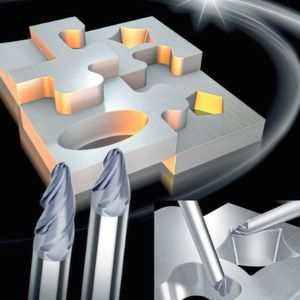
The Curvemax series of Inocatools, a series of solid carbide tungsten carbide rollers in tangential and conical shape, shortens the time required for finishing complex, free surfaces in a wide range of materials.
Inovatools predicts that, compared to conventional ball mills, new Curvemax tools used in the same application can save up to 90%, up to 60%, improved surface quality and up to 90% longer service life. Tobias Eckerle, Production Manager at Inovatools, says CSC’s strategy is an excellent example of joining top-of-the-line CAM software with powerful processor centers and innovative tool development to create pioneering new cutting techniques.
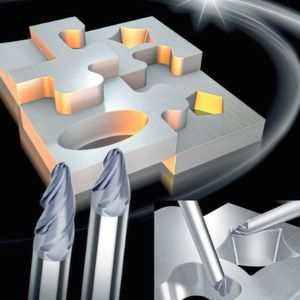
A bigger line distance equals a bigger engagement width
Thanks to their special geometry, the new Curvemax mills from Inovatools permit bigger path distances and line jumps during pre-finishing and finishing. Although the working radius is larger than that of a traditional full-radius mill, the tool still has the same diameter. This leads to a significant reduction in process times. Thanks to the bigger engagement width, the cutting edge does not suffer from wear at any point. Combined with the extremely smooth high-performance coating Varocon, this helps to increase the tool’s service life. The larger and flatter overlap reduces roughness and ensures surface finishes even better than those created by traditional full-radius mills. Inovatools offers the new CSC-Curvemax mills in conical and tangential form as four-edged cutters for finishing in different sizes and radii.
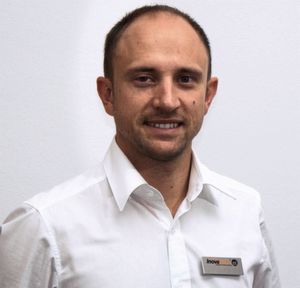
The following real-life example underlines the performance of the Curvemax: While a conventional ball-shaped mill (Ø 6 mm; line distance: ae 0.17 mm) takes 14:53 minutes to finish a workpiece made of tempering steel 1.2379, the Curvemax (conical form; line distance: ae 2.20 mm) takes only 2:34 minutes for the same workpiece. The average raw value with the ball-shaped mill was 0.8 µm – with the Curvemax, it was 0.5 µm.
Tobias Eckerle: “This example clearly demonstrates how powerful processing machines can calculate the optimum path for our new Curvemax mills to ensure high-efficiency machining of level and freeform surfaces. Intelligent automatic systems ensure not only that the tool optimally clings to the workpiece, but also that the potential of the special tool geometry is fully utilized.”
Wide range of applications
Thanks to their curve segment milling technology, the Curvemax mills also open up new production methods. For example, the tools can be used to reliably create undercuts, freeform surfaces and variable setting angles. In addition, complex contours can be pre-finished and finished, even on narrow inside radii. One application is in the aviation and aerospace industry. In addition to the high surface quality and shorter production times, Inovatools states that Curvemax mills considerably increase productivity and cut workpiece costs, for example in the production of turbine blades or the pocket milling of aeronautical components made from aluminum alloys.
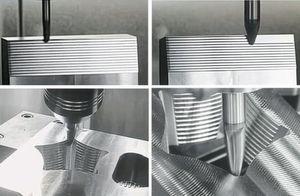
Tobias Eckerle, Product Manager at Inovatools: “In addition to the high surface quality and shorter production times, our CURVEMAX mills considerably increase productivity and cut workpiece costs, for example in the production of components for the aeronautical industry.” (Source: Inovatools)