Formlabs has completely re-engineered its approach to resin 3D printing with the LFS print process – the technology in Form 3 and Form 3L.
Formlabs announced in April that it has expanded its hardware offering with two new, advanced professional low force stereolithography (LFS) 3D printers.
The two new introduction of Formlabs advanced professional low force stereolithography (LFS) 3D printers to its hardware line-up are the Form 3 and Form 3L, which will be among the exhibits at the Formlabs booth at Moulding Expo in Stuttgart.
LFS 3D printing is an advanced form of stereolithography that delivers consistently flawless parts. The LFS process uses a flexible tank to drastically reduce the forces of the peel process, providing incredible surface finish and detail, and linear illumination to deliver accurate, repeatable parts, according to Formlabs.
The company says it has completely re-engineered its approach to resin 3D printing with the LFS print process, the technology in Form 3 and Form 3L. With these two new printers, the company has taken another huge leap forward with LFS 3D printing, improving print quality and reliability, while still offering a powerful and affordable 3D printer on the market.
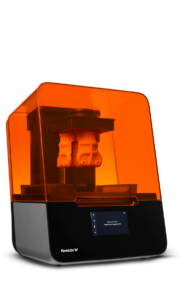
Among the benefits of the LFS process are high detail and surface finish, thanks to a flexible tank that reduces forces on parts during printing. Also, its light processing unit maintains a uniform, high density laser spot to ensure accurate, repeatable prints, enabling pin-point precision. Easy clean-up and smoother parts with tear-away, light-touch supports are available. Integrated sensors help maintain ideal print conditions and send users alerts on the state of the machine, thus providing non-stop printing. Remote printing is made possible via its online dashboard and Formlabs offers constant uptime with upgradeable and modular components.
Form 3L simultaneously uses two LPUs to bring large format 3D printing in-house. It offers five times the build volume and two times the laser power of the Form 3 to print large parts fast.
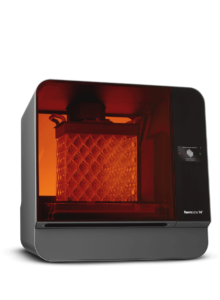
Furthermore, the company also announced a new material – draft resin, which is said to print at 300 microns layer lines and is three to four times faster than other standard resins, making it ideal for rapid prototyping.