RESEARCHERS TO OPTIMIZE LIQUID METAL CASTING WITH MATHEMATICAL MODEL
Scientists at Aston University have launched a project to develop a mathematical model to improve the liquid metal casting process.
The approach is hoped to prevent lightweight aluminum alloys from quickly oxidizing when first exposed to air. The UK-based researchers believe that greater knowledge of this could improve the process of 3D printing with light metals.
This research will be funded by a £80,000 grant from the Engineering and Physical Sciences Research Council (EPSRC), and is being led by Dr Paul Griffiths, a Senior Lecturer of applied mathematics based in the university’s College of Engineering and Physical Sciences.
Starting in April 2024, this 12-month project is titled ‘Developing an accurate non-Newtonian surface rheology model,’ and will be conducted in partnership with the France-based Grenoble Institute of Technology (INP).
“The aim of this investigation is to develop a mathematical model that accurately captures the two-way coupling between a liquid metal flow and the oxide layer above, with the latter behaving as a non- Newtonian liquid/gas interface,” – explained Dr Griffiths.
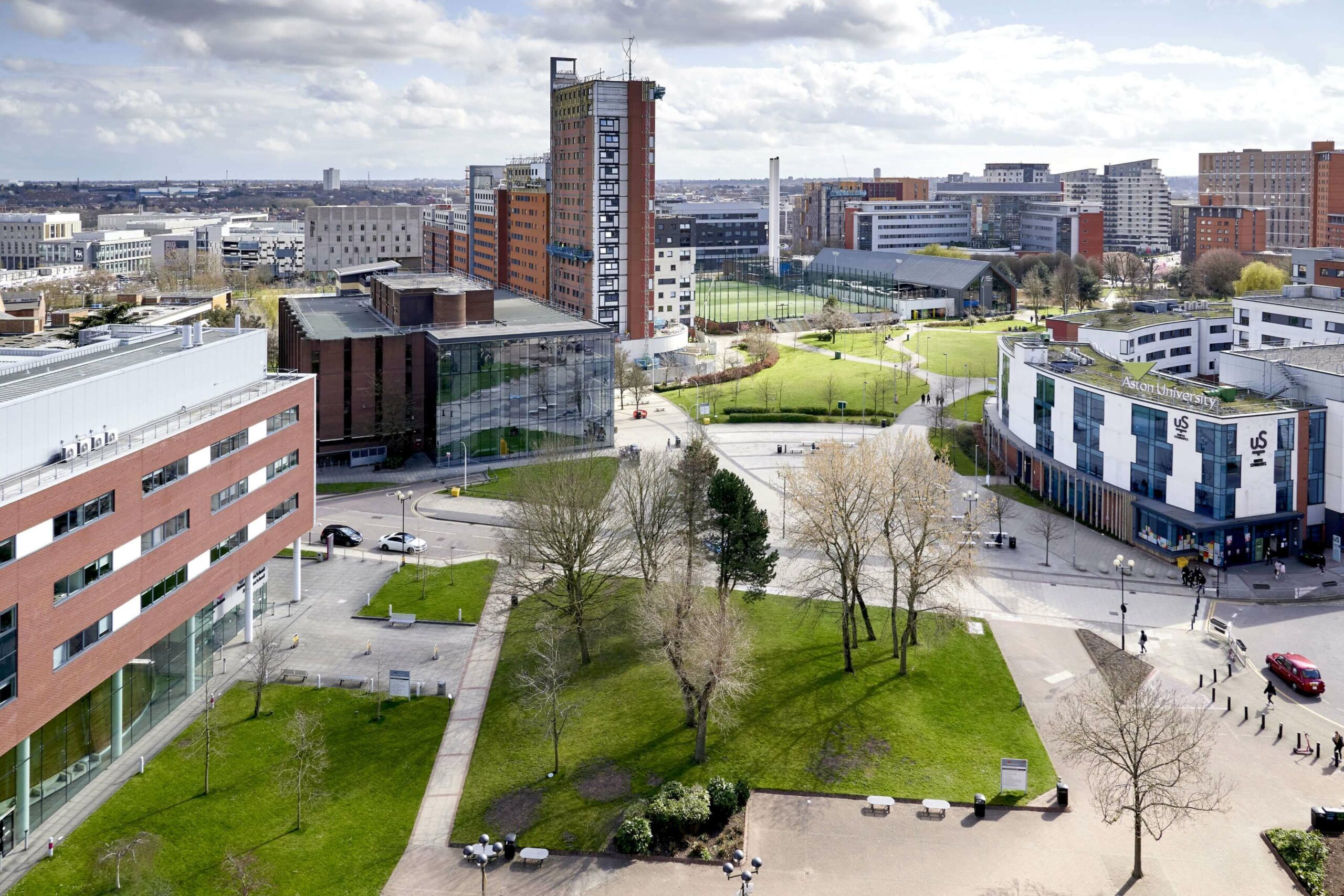
Improving liquid metal casting with mathematics
The transportation industry is currently seeing traditional metals such as steel be replaced by lighter alloys.
One key benefit of this shift away from steel is the fact that such alloys don’t rust. However, light alloys quickly oxidize when first exposed to ambient conditions. This negatively impacts their quality and lifespan, limiting their utility in industrial manufacturing applications.
In order to overcome these challenges, the research team will focus on the thin oxide films that develop on alloys. Whilst these films do act as a layer of protection from outside conditions, helping to protect against corrosion, they pose problems.
During the casting process, when the aluminum is in a molten state, the thin oxide films can become encapsulated into the liquid metal flow. This encapsulation process can occur many times, and leads to the embedding of oxide films into the final product, diminishing the quality and fatigue life of the casted parts.
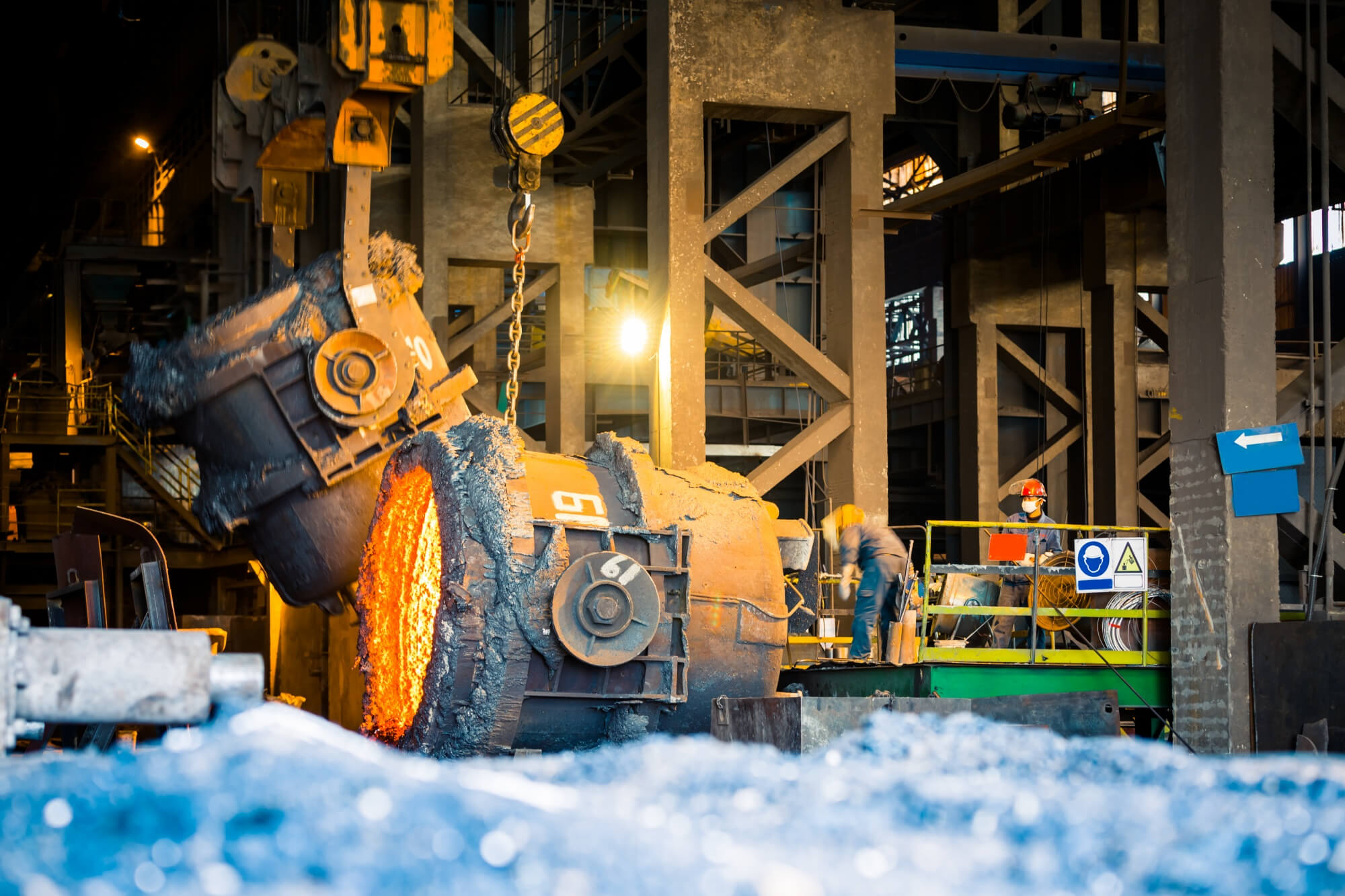
According to the researchers, gaining a greater understanding of how to control this oxidizing process will help to reduce costs associated with the production lifecycle. The researchers argue that this will result in greater demand for lightweight alloys, and a reduction in greenhouse gas emissions, given that less energy is required to transport a lighter product.
The ultimate goal of this project is to develop a mathematical model capable of accurately describing the dynamics between the liquid metal flow and the oxide layer, something which cannot be determined using current methods.
“The objective of this project is to describe both the surface characteristics – velocity and shear profiles – as well as the important effects of surface curvature.” – stated Dr Griffiths. “The benefit of a more appropriate mechanical model for the oxidized surface of a melted metal flow would lead to a better understanding of the encapsulation process which affects the alloy.”
It is hoped that the findings will offer new insights into how to control this oxidization process in a practical setting. The mathematical model will be validated and verified against existing experimental observations.
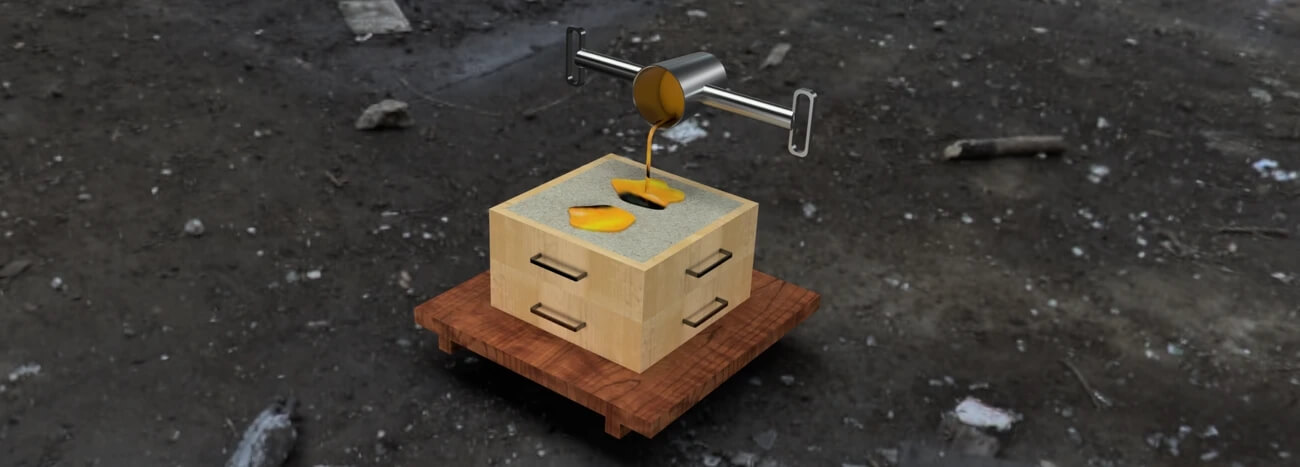
Research in metal additive manufacturing
Research into improving metal additive manufacturing is nothing new. Last year, a team of researchers from multiple institutions, including the National Institute of Standards and Technology (NIST) and KTH Royal Institute of Technology in Sweden, announced a breakthrough in the understanding of how cooling rates impact metal properties during laser powder bed fusion (LPBF).
Scientists have previously struggled to produce metals which possess specific, predetermined, crystal structures. Consequently, metal 3D printing frequently produces parts with complex shapes that crack prematurely. This study examined how cooling rates impact the crystal structure of metals, with the goal of controlling the microstructure of metal during the initial steps of 3D printing.
Solidification Model
Ultimately, the scientists’ findings validated the predictions made by a computational model that describes the solidification of alloys, called the Kurz-Giovanola-Trivedi (KGT) based solidification model. As such, the study indicated that this model can be used to predict and control metal parts during 3D printing, improving the consistency of large-scale manufacturing.
Elsewhere, researchers from Tsinghua University and the National University of Singapore have investigated the effect of fluid flow on the mechanical properties of metal 3D printed parts. Tree-like structures of crystals, called dendrites can grow and propagate as molten metal solidifies. As they grow, dendrites can negatively impact the mechanical properties of metal.