Welding products expert Lincoln Electric Co. is moving into additive manufacturing.
But the way Lincoln Electric does additive manufacturing makes use of its expertise. Essentially, the company is “welding layer upon layer upon layer upon layer” of metal onto itself, creating predetermined shapes, explained Mike Whitehead, president of Lincoln Electric’s global automation, cutting and additive businesses.
It may sound like a simple concept, but it’s difficult to perfectly layer those welds and make sure the layers are bonding correctly. And Lincoln Electric already makes the products needed for the process: the wire consumable, the controlling software and the automated welding equipment.
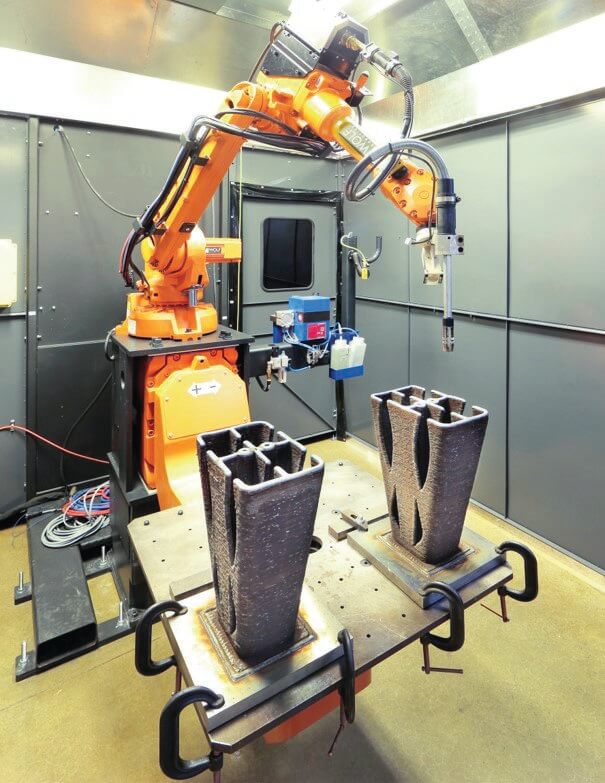
“There’s a lot of challenges that go in with that, and there’s really no better company in the world to do it than a company that has expertise in welding,” Whitehead said.
Lincoln Electric has been working in large-scale metal additive manufacturing for about five years, but it was in more of a research-and-development function, Whitehead noted. Its newly established metal additive manufacturing service business will formalize Lincoln Electric’s role in the space. The formal launch will take place in mid-2019.
Previously, Lincoln Electric had been doing work in its automation building and at Oak Ridge National Laboratory. But now, the company is in the process of building out a new additive manufacturing center at 26250 Bluestone Blvd. in Euclid, by the company’s headquarters. Lincoln has a long-term lease for the approximately 75,000-square-foot building, Whitehead said.
The buildout started at the end of 2018. About a third of the building is already completed with office space and some existing robotic weld cells. Whitehead said more robotic weld cells, where the additive manufacturing is actually done, will be added in the next three years.
Lincoln Electric has a group of about 10 engineers working in the additive manufacturing space, but Whitehead said he expects that to ramp up quickly as the business expands.
The metal additive manufacturing parts being made by Lincoln are large: excavator arms, propeller blades. For example, an excavator arm may be seven feet tall and 600 or 700 pounds, Whitehead noted. In comparison, products made through metal powder 3D printing tend to be much smaller, he said.
There are different benefits to making those large parts in this way. For example, Whitehead said Lincoln Electric had been approached by the military in the past. The Navy was looking for a way to minimize the number of tools it needed to transport in order to fix its equipment. Large-scale metal additive manufacturing would let them take one robot that could make what they needed on site, he said.
Customers can get their parts in less time — sometimes within days as opposed to months, Whitehead said — and the parts can be made with less waste. Large parts can be expensive to fabricate because they need to start with far more raw material than ends up in the part. With additive manufacturing, the products can be printed close to the final dimensions.
The products still need some machining after they’re printed, said Whitehead. That’s where the company’s recent acquisition of Michigan-based Baker Industries Inc. comes into play, allowing Lincoln to serve as a single-source supplier for customers. Baker does both large- and small-scale machining, Whitehead said, often serving the automotive and aerospace industries.
“From beginning to end now, we can really handle that,” he said.
Baker also uses plastic 3D printing in its work and can bring that expertise to Lincoln Electric.
While a lot of what Lincoln Electric has been doing so far has been creating experimental or prototype parts, Whitehead sees a lot of opportunity in additive manufacturing. And he thinks the large-scale metal parts market has been neglected.
Lincoln Electric isn’t the only local entity that sees opportunity in this announcement.
Lincoln Electric’s expansion into this space supports Northeast Ohio’s becoming a “center of excellence” for additive manufacturing, said Jay Foran, senior vice president of industry and innovation at Team NEO. Additive manufacturing is one of the technologies Team NEO has focused on supporting in recent years. Being able to provide different types of additive manufacturing with different kinds of materials, from metal to polymer to ceramic, is a benefit to the region.
Additive manufacturing, and the companies that are spinning out, starting up or maturing into the space, represents a “huge opportunity for Northeast Ohio,” said Rob Gorham, executive director of America Makes, the National Additive Manufacturing Innovation Institute in Youngstown. This kind of expertise is going to make what he called the “Tech Belt” of Northeast Ohio and western Pennsylvania more competitive.
Lincoln Electric is a member of America Makes and has worked on some of the institute’s projects.
Gorham said he hopes to see “Lincoln Electric times 100,” building a deep competency in the state rather than “one-off capabilities.” He said that’s what will help the state be successful as manufacturing becomes more digitized.
“So Lincoln Electric’s just on the forefront of that,” Gorham said.