Cubicure and Evonik cooperate in the development of photopolymers for additive manufacturing.
Cubicure and Evonik Industries announce a strategic R&D cooperation in polyester resins for additive manufacturing. The objective of the joint project is the development and production of an innovative 1K-resin system for the Hot Lithography technology. At the leading global exhibition for additive manufacturing, the Formnext 2019 in Frankfurt, first results will be presented to visitors in midNovember.

Source: Cubicure
The joint development project of Cubicure and Evonik focuses on highly viscous polyester resins, which for the first time become processable using the Hot Lithography (HL) technology. With the HL, Cubicure offers a unique manufacturing process in the 3D-printing industry. The heated stereolithography process (SLA) allows the processing of high molecular and therefore highly viscous resins. This feature expands the chemical process window compared to previous SLA processes for the development of new and innovative polymer materials and creates the potential for completely new material system concepts in the field of photopolymers.
Evonik, a pioneer in the field of plastics for additive manufacturing, has recognized this potential for innovation and thus, is using Hot Lithography as a development platform for light-curing polyester resins. ‘The Hot Lithography technology developed by Cubicure is an interesting option for manufacturing components that meet the exacting standards of industrial applications,’ Prof. Stefan Buchholz, the executive director of Evonik Creavis GmbH, says. ‘We have been using this platform for the development of next-generation light-curing resin systems for a while. For this purpose, we rely on internally supplied, custom-made components such as oligomers, specialty monomers and suitable additives.’
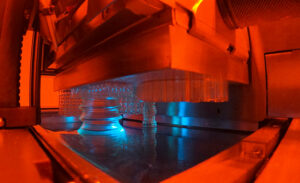
Source: Cubicure
Innovative 1K resin
As one of the world’s leading group in specialty chemicals, Evonik uses its material expertise in polyester resins to develop an innovative one-component resin system (1K) in collaboration with Cubicure’s process experts. Unlike 2K systems, a 1K system requires no mixing procedure right before use and can be applied directly in the printing process without a limiting pot life.
This ensures continuous, uninterrupted and process safe production of additive manufactured parts. ‘The joint strategic development project with Evonik is already in an advanced state. We are pleased to expand our material portfolio by flexible photopolymers in the future. A 1K system based on polyesters is an important building block on our way to stable and scalable additive production processes,’ Robert Gmeiner, CEO and co-founder of Cubicure, emphasizes.
Elastomer-like properties:
The developed polyester resin enables the additive manufacturing of complex components with elastomer-like material properties. This allows applications, which are known until now e.g. from TPC processing by injection molding such as:
- Sealings, grommets, bellows
- Shock absorbers, protective covers
- Shoe soles, protectors, handles, etc.
Visit Cubicure at Formnext in hall 11.1, booth D.48 from November 19-22, 2019 in Frankfurt.