DPS Software, IT system house with focus on digital solutions for the manufacturing industry, presents itself at the Intec 2019 with three main topics: Design solutions with Solidworks CAD and production-related solutions in CAD, manufacturing software CAM using SolidCAM as well as the simulation of factories and manufacturing plants with Visual Components.
This year the software offers increased speed, which presents itself particularly time-saving for users with complex building groups. Solidworks also achieves improved performance through the use of graphics technology. In interaction with modern graphics cards, whose GPUs achieve large computing capacities, pin-sharp and flowing images of the high quality are produced.
Reliable software solutions that are constantly optimized and fully harmonize with the existing software are important for the user. DPS software provides the user with competitive advantages through fully integrated solutions from the idea to the design, including clamping and production technology, CNC programming, tool management, data transmission to CNC machining including subsequent quality assurance. This can be done smoothly by consultants who understand the entire process chain and help to avoid isolated solutions.
SolidCAM, an innovative market driver for the latest quality standards and methods such as iMachining, has improvements in the current release that will be explained at the booth.
These include job templates and template groups that can be dragged and dropped to edit the desired part. The new technology type Multi-tools helps to group together machining steps that build on each other in order to initially combine separate jobs for roughing, rough finishing and finishing. In addition, the latest developments in tool technology such as circular segment milling cutters can now also be used for programming. In addition, it is now possible to control sliding headstock lathes for special components.
The further development of existing systems is also part of SolidCAM’s future strategy. The user finds a newly designed material database as well as the new Turbo HSM for extremely fast tool path calculations.
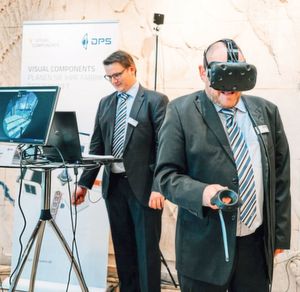
Live demos: At the Intec, these innovations will be presented hourly, including live milling, with the booth neighbor and partner Hurco. The tools come from Stock. Factory and manufacturing simulation with the latest VR technology
The 3D factory simulation from Visual Components enables both professional factory planning and the creation of a virtual twin for cycle time analysis. This means that the user has the possibility to perform a realistic “walk” through his virtual factory or plant. Virtual twins of the plant can be created by connecting virtual or real controls. With these it is now feasible to carry out tests in a cost- and resource-saving manner.
In this way, machine park variations can also be better assessed in the context of the hall layout and optimally included in the process planning.
The second main pillar of the software is robot programming, which can be fully integrated into plant planning. With this, a robot space path curve can be automatically generated using a 3D CAD contour and then transferred to various real robots for welding and grinding processes via a postprocessor.
At the Intec the visitor can experience live the possibilities of the virtual reality of Visual Components Experience. They will be able to walk through a virtual factory and observe processes in real time.