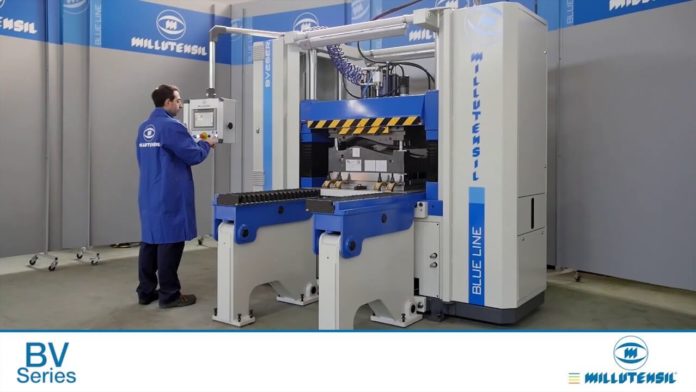
Italy-based spotting presses manufacturer, Millutensil, has rounded out its machine programme offerings.
Spotting presses manufacturer, Millutensil, says the constantly increasing demand for plastic products made of two or three-component plastics has grown to become a big challenge for the mould industry the last few years. With moulds getting bigger and more complex, the required quality standards have also significantly risen.
MD Beatrice Just noted: “Over the last few years, our customers frequently asked for presses, of which their operation was similar to those of the injection moulding process.” She added that the demands made on mould makers and the plastic injection moulding sector have considerably increased, just like the demands of Millutensil’s customers.
To meet customers’ needs, the company has expanded its range of presses with down and upwards rotary tables. Not too long ago, the smallest plate dimensions were 1,200mm x 1,000mm, while the biggest were 2,500mm x 2,000mm.
Today, Millutensil offers plate dimensions of 980mm x 850mm as in the BV26E-RG model and plate dimensions of 3,500mm x 2,400mm for the MIL305 model. Additionally, the latter provides a clamping force of 400t. Furthermore, the MIL product line is the premier among the spotting presses, thanks to its four hydraulic cylinders that evenly distribute the clamping force over the whole plate surface in order to obtain the best contact pattern.
„No matter what the future holds for the international mould industry, we still want to remain an innovative and resourceful partner for our customers and always pay particular attention to the challenges they want us to address” explained Beatrice Just.