Artificial intelligence (AI) is poised to make industrial equipment predictive maintenance truly predictive.
A machine tool builder is using artificial intelligence technology to predict when a spindle problem might occur, so shops can better prepare for and schedule necessary maintenance.
One of examples is Mazak’s AI-based Spindle Health Monitoring System (SHMS) that is currently an option for its HCN horizontal machining centers (HMCs).
Mazak’s SHMS was created to enable shops to take spindle maintenance measures long before spindle or spindle bearing damage occurs, minimizing downtime and enabling any maintenance tasks to be more conveniently scheduled.

Joe Sanders, process development coordinator for Mazak, says the key difference between the company’s AI-based system and other spindle monitoring technology is that the SHMS is not based on threshold data. That would be the case in which an alert would be sent when a specific spindle vibration frequency is detected that would suggest damage has already or is very soon to occur. Instead, he says the SHMS can detect issues months before they happen, providing time to schedule spindle repair or replacement at the most convenient time.
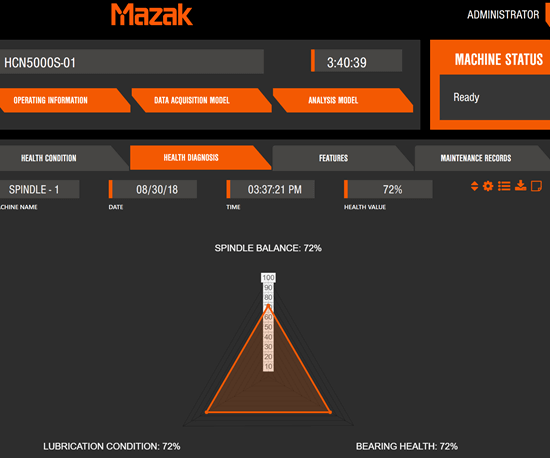
Source: Mazak
Data crunched from one year of extensive spindle destructive tests led to the creation of the SHMS’s AI spindle neural network self-organizing maps, spindle-specific signatures that can determine the difference between good vibrations and bad ones. Algorithms created from these maps predict how spindles will degrade over time (barring a crash) while displaying remaining lifespan as a percentage. This differs from estimating a timeline of a spindle’s life, because we don’t know if a machine will be used for light-duty work, heaving cutting, 24/7 operation or any other possible scenarios.
The SHMS’s primary components include vibration and current sensors, a data acquisition module, and an industrial computer to process the SHMS algorithm. Upon installation, a one-hour modeling test maps that particular spindle’s operating signature. After that, users can perform periodic 60-second tests that compare data to the spindle model. When cycle times are sufficiently long, we suggest performing a test after each part is completed. However, this likely is not necessary for parts with relatively short cycle times.
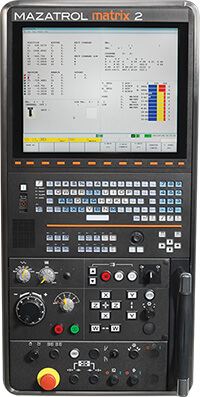
Source: Mazak
The SHMS is available as an option on Mazak HCN machines equipped with the company’s Smooth CNC and as a retrofit for those machines with Matrix CNCs. (The system’s graphical user interface is currently being refined.)