The RigiMill high-speed machining centre from Swedish manufacturer Modig holds the world record for high-speed milling. The Y and Z axes of the RigiMill feature twin drives with cooled HMD ball screws from NSK. Axial bearings and roller guide-ways for the axes are also supplied by NSK.
For machining centres in the aircraft and aerospace industries, chip removal speed is a key parameter because many of the central, very large components like wing ribs and other structural parts are milled from solid material. For example, parts weighing over 100 kg could be made from blocks of aluminium weighing 4 tonnes or more, which means that 97.5% of the material has to be removed.
Modig Machine Tool AB in Virserum, Sweden is well placed in the demanding field of high-speed machining for materials such as aluminium, titanium, steel and composites. The company, develops and manufactures very high performance CNC machines that are used by aerospace manufacturers all over the world, including Airbus, Boeing, SAAB, Sikorsky and Volvo Aero.
“One of our goals was to develop the first 2-in-1 machine in this performance class; in other words a milling machine for high-speed roughing and finishing,” explains David Modig. “And the second goal: the RigiMill had to be the fastest milling machine in the world.”
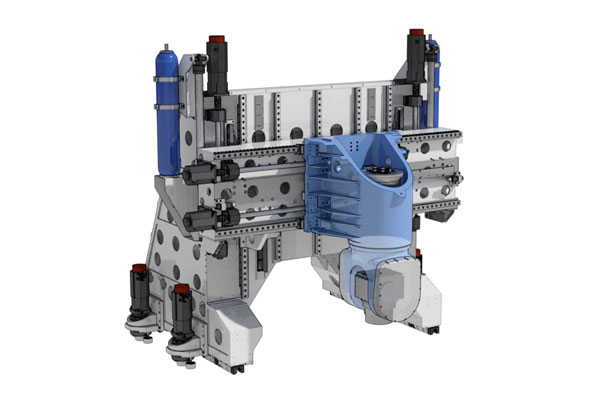
This goal was not an end in itself and the purpose was not to get an Olympic medal. David Modig says: “The aircraft industry is booming and manufacturers are continuously expanding their capacity, so we wanted to supply our customers with gantry systems that have even shorter machining cycles.” Machining the structural components of an aircraft also requires precision at the highest level, so the stiffness of the machine axes is just as important as speed, or even more so. The spindle of the RigiMill therefore uses twin drives on the Y and Z axes with a positioning accuracy of 0.5 μm in each case. The two electric motors work in master/slave mode.
When selecting the linear drives for the axes, the decision was based not only on the technical specifications of the drive units, as David Modig explains: “We only work with the best suppliers. In this case we looked for a reputable supplier who had drive units with the highest accuracy, and the passion to support and promote innovative developments.”
With these criteria in mind, the choice was made in favour of NSK. And it was no surprise, because all previous models of Modig machining centres have been equipped with NSK drive components. In co-operation with Swedish authorised distributor Acumo, specialists from NSK in Ratingen configured the drive units, taking into account factors such as torque, speed, axis acceleration forces and the temperatures generated in the spindle drives during high-speed machining.
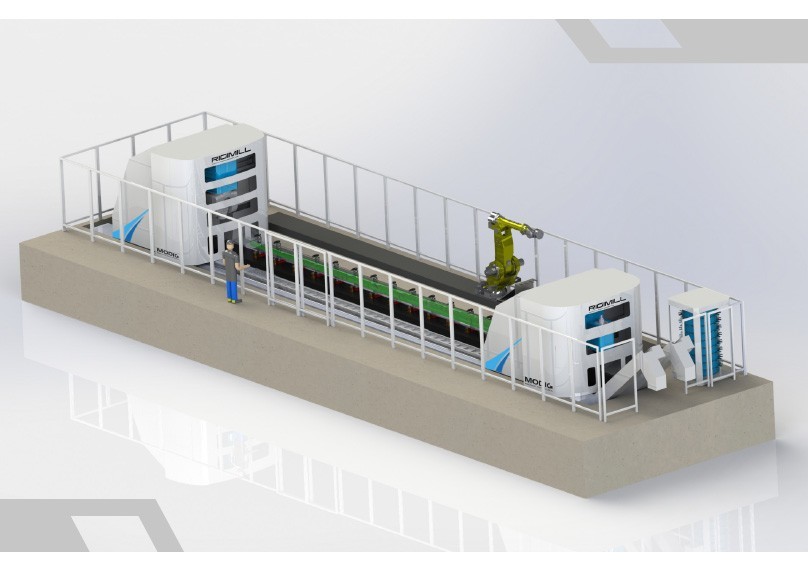