Using commercially available systems, a group of researchers from The Johns Hopkins University have managed to fabricate Ultra-high-temperature ceramics (UHTCs). The materials have been traditionally difficult to print, but thanks to the new research, that may be about to change.
UHCTs
UHCTs are refractory ceramics that are notable for their high stability in ultra high temperatures (hence the name). They are ideal candidate structural materials for applications that require resilience to extreme temperatures (>2000°C), such as thermal protection products or bulk materials for the fabrication of heating elements.
In addition to being great at resisting high temperatures, they are well suited for situations where the components may be subjective to high mechanical loads, or aggressive oxidizing environments.
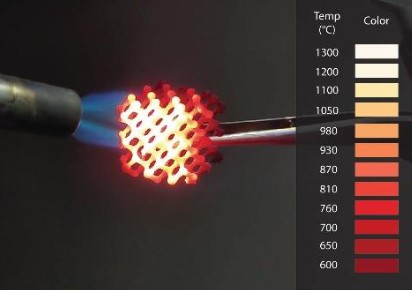
The researchers have been developing a method to 3D print one type of UHTC in particular, namely those using titanium carbide (TiC), which is an extremely hard refractory ceramic material, similar to tungsten carbide.
It has been difficult to fabricate TiC structures with AM in the past, largely because the strong covalent-ionic and metallic bonds in the materials slow atomic diffusion that prevents sintering.
Dry powder and colloidal shaping manufacturing processes have proven complex to get right, and as a result, high post-processing temperatures and pressure-assisted techniques are needed to produce dense components with these materials. And as these processes are non-additive, they lack the benefits of AM, such as the ability to produce complex geometries.
Using commercially available systems such as a plastic LPBF system and a tube furnace, the research team was able to produce UHTC cubes and lattices with sub-millimeter resolution, thus proving that it can indeed be done with AM.
The Process
The first stage was to use an SLS system (a Sinterit Lisa Pro) to sinter a titanium precursor mixed with a polymer binder, to produce the green part. The sealed build chamber was modified for compatibility with Argon gas and fitted with a dynamic O2 monitoring device to prevent Ti oxidation.
Next, the green parts were subjected to isothermal gas-solid conversion in the tube furnace in CH4 (methane) to form TiCx structures. In other words, pyrolysis of the polymer binder resulted in the generation of enough carbon to facilitate the transformation of Ti into TiCx.
To complete the reaction into TiC, further processing was needed.
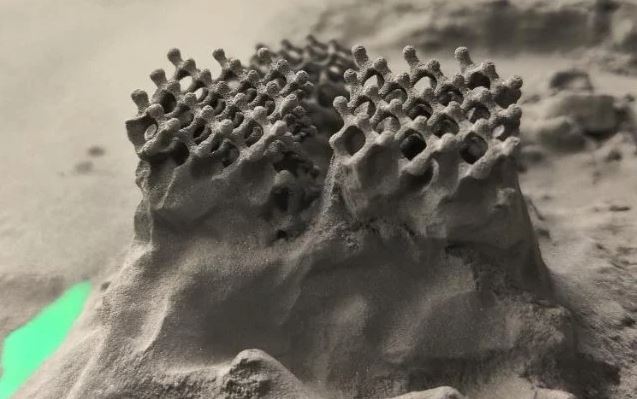
The researchers opted for two different print geometries to assess different qualities of the finished parts. They printed a 1.5 cm x 1.5 cm x 1.5 cm cube (to assess the influence of anisotropic volume changes, part density, and CH4 penetration) and a lattice structure (to assess resolution and precision).
Here are some fun facts about TiC-based UHCTs.
TiC has an extremely high melting point (3067 °C), and the highest hardness of any carbide. It also has the highest compressive strength of any known material, as the image of the printed lattice below demonstrates quite nicely.
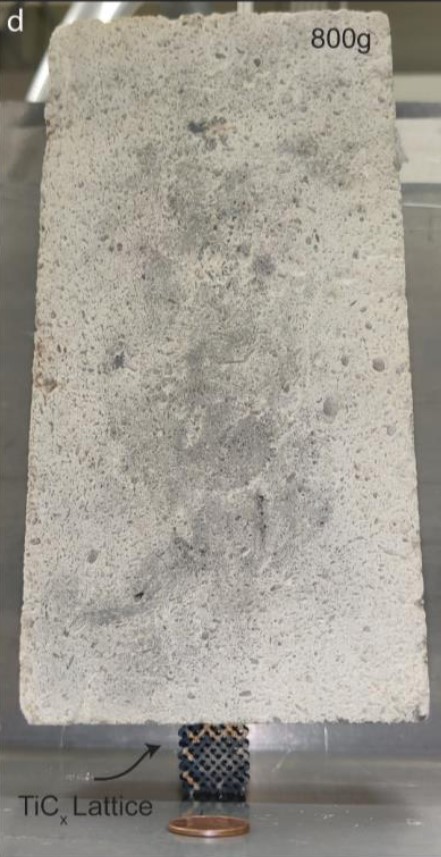
Could be applied to other carbides such as ZrC, HfC, or TaC that have been difficult, if not impossible, to fabricate with AM.