The transition to a low-carbon world requires a transformation in the way we manufacture iron and steel. There is no single solution to CO2-free steelmaking, and a broad portfolio of technological options is required, to be deployed alone, or in combination as local circumstances permit. This series of fact sheets describes and explores the status of several key technologies and initiatives and issues.
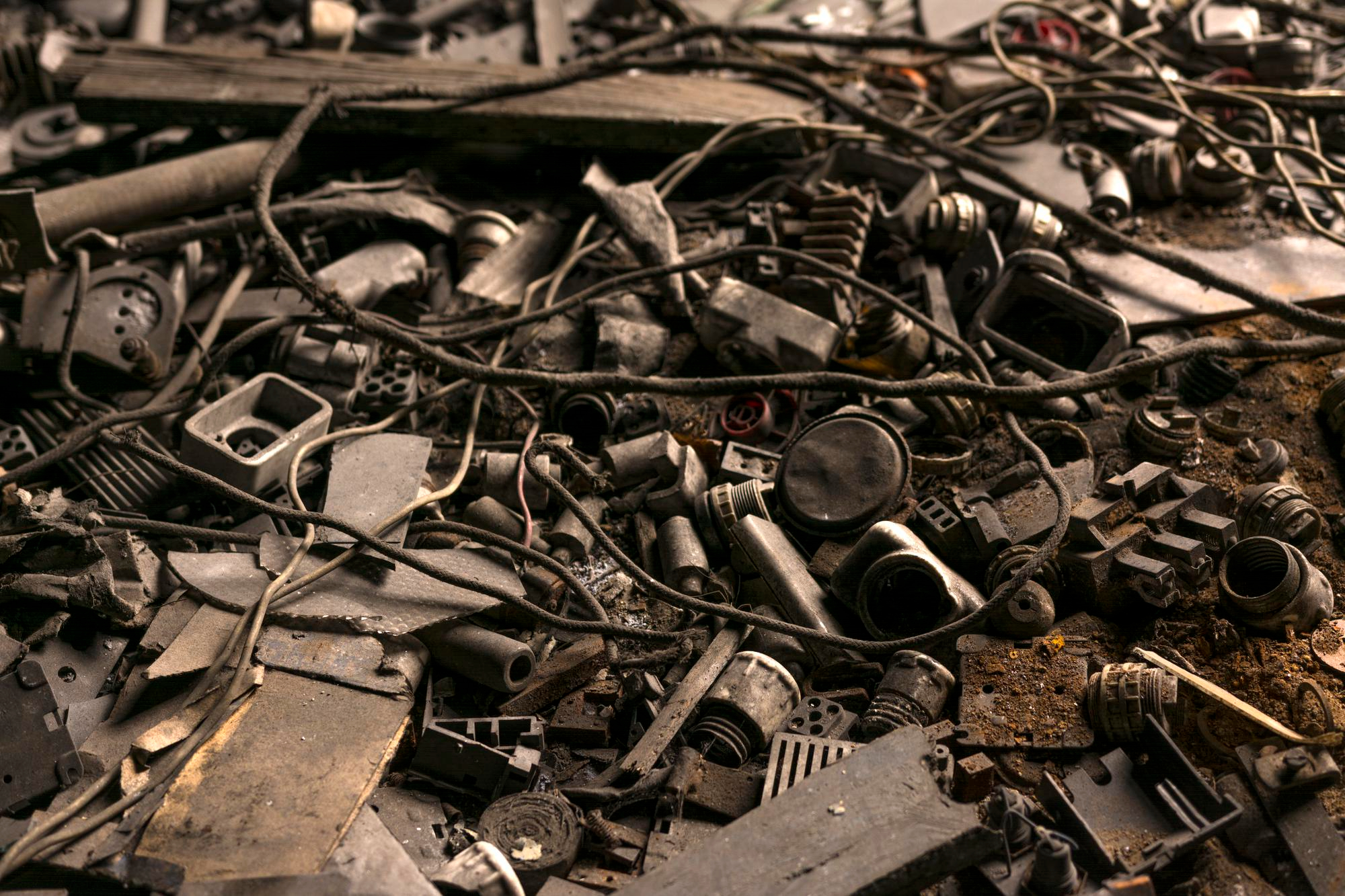
What is scrap and why is it important?
Scrap is a term used to describe steel that has reached the end of its useful life, known as ‘post-consumer scrap’ or has been generated during the manufacture of steel products, known as ‘pre-consumer scrap’.
While the term ‘scrap’ may lead one to believe this is a waste product, it is actually a valuable raw material used in every steelmaking process.
Due to its inherent magnetism, steel is very easy to separate and recycle, making steel the most recycled material in the world.
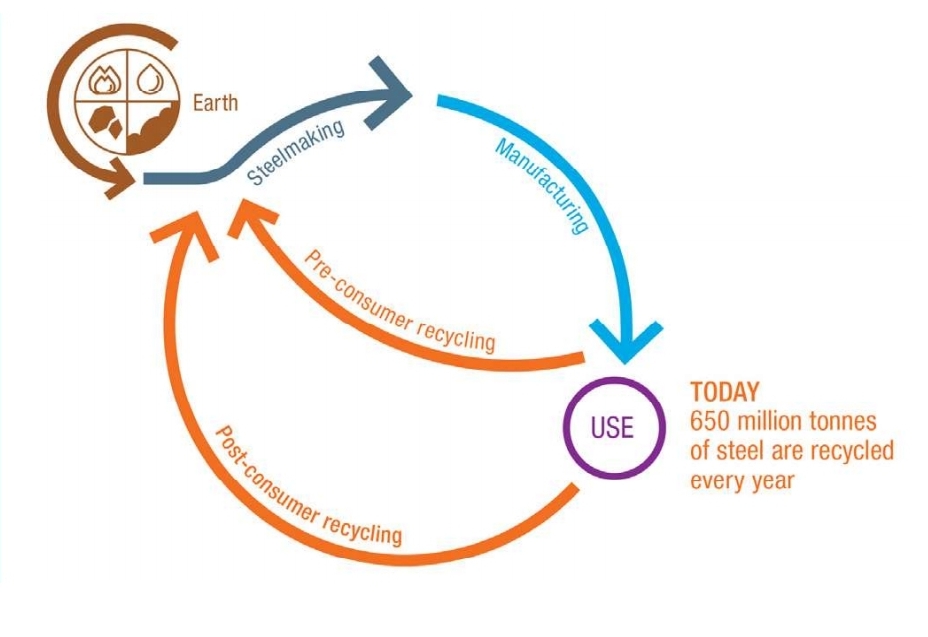
How and why is scrap used?
Steelmaking has two main metallic inputs: iron ore and recycled steel scrap. Around 70% of the total metallic input to steel production globally is derived from iron ore, with scrap making up the rest.
Melting steel scrap at the end of its useful life allows us to create new steels, making adjustments to the chemistry and shape of the new product
Scrap steel is separated and sorted, and can be used to make any new steel product.
Every steel plant uses scrap as part of its raw materials mix, and therefore every steel plant is also a recycling plant.
In blast furnace (BF) steelmaking, each charge of the basic oxygen furnace, in which carbon carbon-rich pig iron is refined into crude steel, typically contains 15%-25% scrap. Scrap acts as a cooling agent, absorbing excess heat from the exothermic decarbonisation process, and also as a source of iron units. In some cases, scrap is added directly to the BF as a source of iron units, reducing greenhouse gas emissions.
In electric steelmaking, electrical energy is used to re-melt charges of up to 100% scrap to make new steel products.
What are the benefits of using scrap?
Scrap plays a key role in suppressing industry emissions and resource consumption, every tone of scrap used for steel production avoids the emission of 1.5 tons of CO2, and the consumption of 1.4 tons of iron ore, 740kg of coal and 120 kg of limestone.
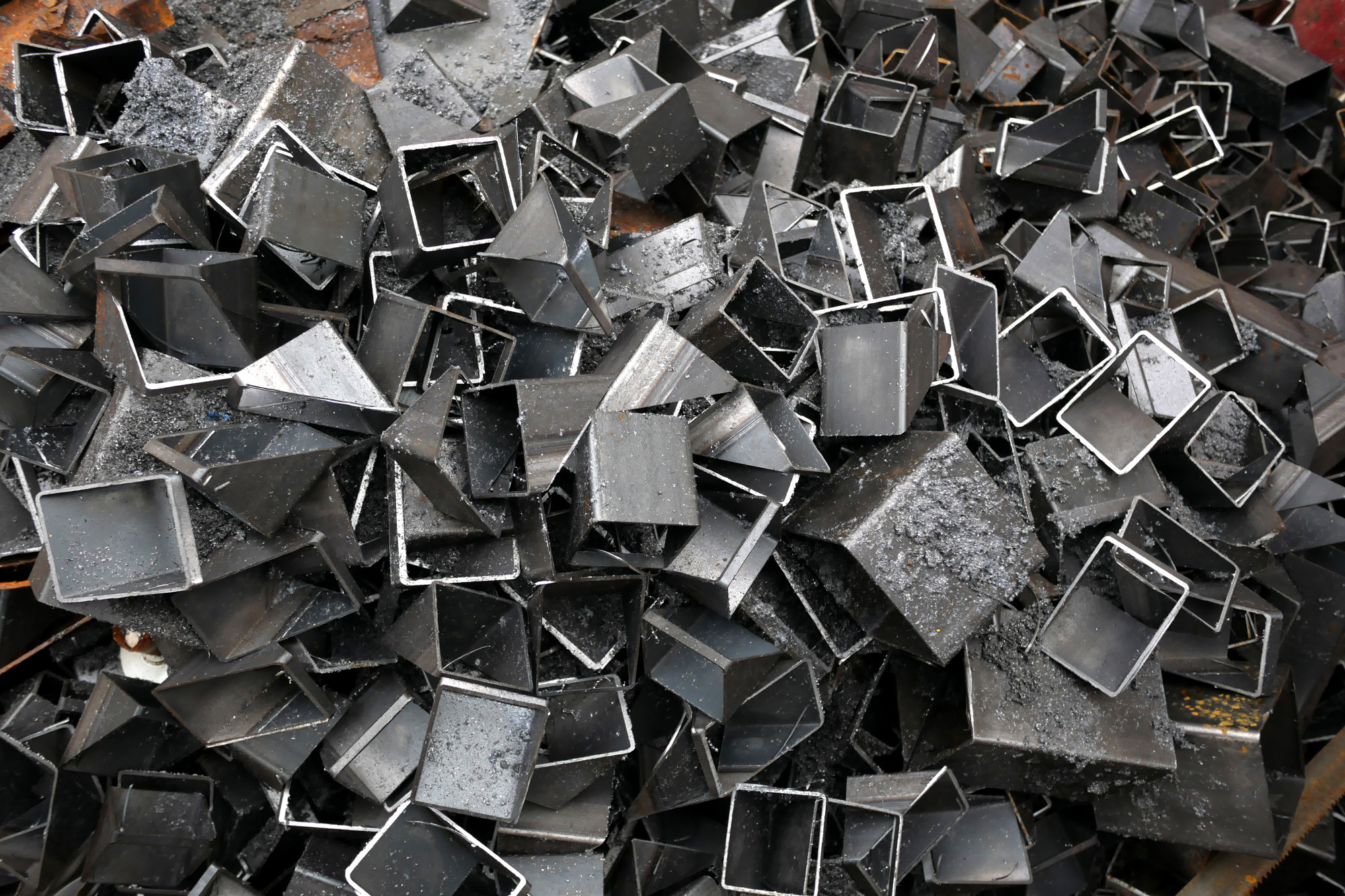
How much scrap is used?
All the scrap that is available to the steel industry is used repeatedly to create new steel. Recycled steel maintains the inherent properties of the original steel and the quality can also be improved on recycling.
Around 650 Mt per year of scrap is consumed each year for steel production (compared with a total crude steel production volume of 1,869 Mt per year), with comparable amounts of scrap used in the primary and secondary routes. This avoids the emission of approximately 975 MT of CO2, annually and significantly reduces the use of other natural resources use, such as iron ore, coal and limestone.
Worldsteel estimates that the global foundry sector uses about 70 Mt of ferrous scrap each year. With a total of 720 Mt, ferrous scrap recycling constitutes the largest recycling activity in the world.
How much scrap is available?
In theory, all new steel could be made from recycled steel. However, currently, this is not feasible due to the scarcity of scrap. This is because of the long service life of steel products, given steel’s strength and durability.
The average life of steel products ranges from a few weeks for steel packaging to up to 100 years for buildings and infrastructure. The average lifespan of a steel product is 40 years. This means there is a significant delay between steel being produced and being available for recycling. Continued growth in steel demand means that transitioning the industry to entirely scrap based production is unlikely to be possible during this century.
Steel demand is growing at a faster rate than scrap is being released from the pool of ‘steel in use’. All scrap currently collected is recycled. As such there is only limited scope to increase scrap availability. Any future increase in availability will be drawn from the expected increase of post-consumer scrap availability.
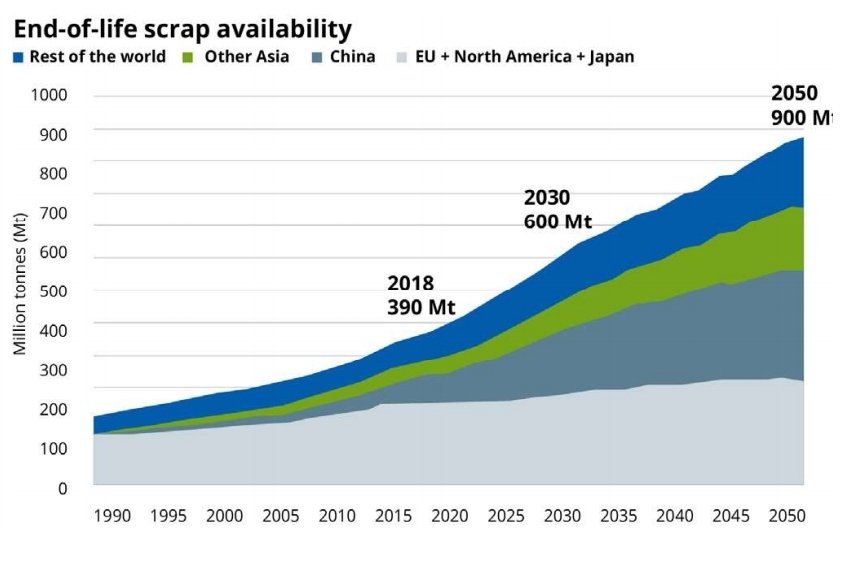
Global steel production increased significantly in the early years of the 21st century, largely driven by growth in China. End of life steel scrap is expected to increase from the mid 2020s as this material starts to reach the end of its life.
While iron ore supply can flex with demand, the availability of scrap is mostly fixed, a function of steel demand and arising of scrap at the end of life of steel products, equipment, and facilities. Worldsteel estimates suggest that global end-of-life ferrous scrap availability stood at about 400 Mt in 2019. We expect that global end-of-life scrap availability will reach about 600 Mt in 2030 and 900 Mt in 2050, a growth of more than 500 Mt in one of our main steelmaking raw materials in the next 30 years.
Looking forward, the continued growth of the circular economy may lead to further extensions in the useful life of steel products through reuse and remanufacturing, suppressing scrap availability below current expectations.
How is scrap quality assessed?
There are several regional classifications used to classify scrap – for example, the The EU-27 Steel Scrap Specification’ developed by EFR, the European Ferrous Recovery and Recycling Federation and the ISRI specifications developed by the Institute of Scrap Recycling Industries, including in the US. Given the international nature of scrap trade, it would be preferable if stakeholders could agree on a global classification to make best use of the expected strong growth in scrap availability and use.
Could build up of tramp elements render some scrap not usable?
The steelmaking process is able to remove most impurities that may be present in scrap steel. Hence ‘downcycling’ of steel scrap into lower quality products is not an issue for the steel industry in the same way it can be for glass and aluminium.
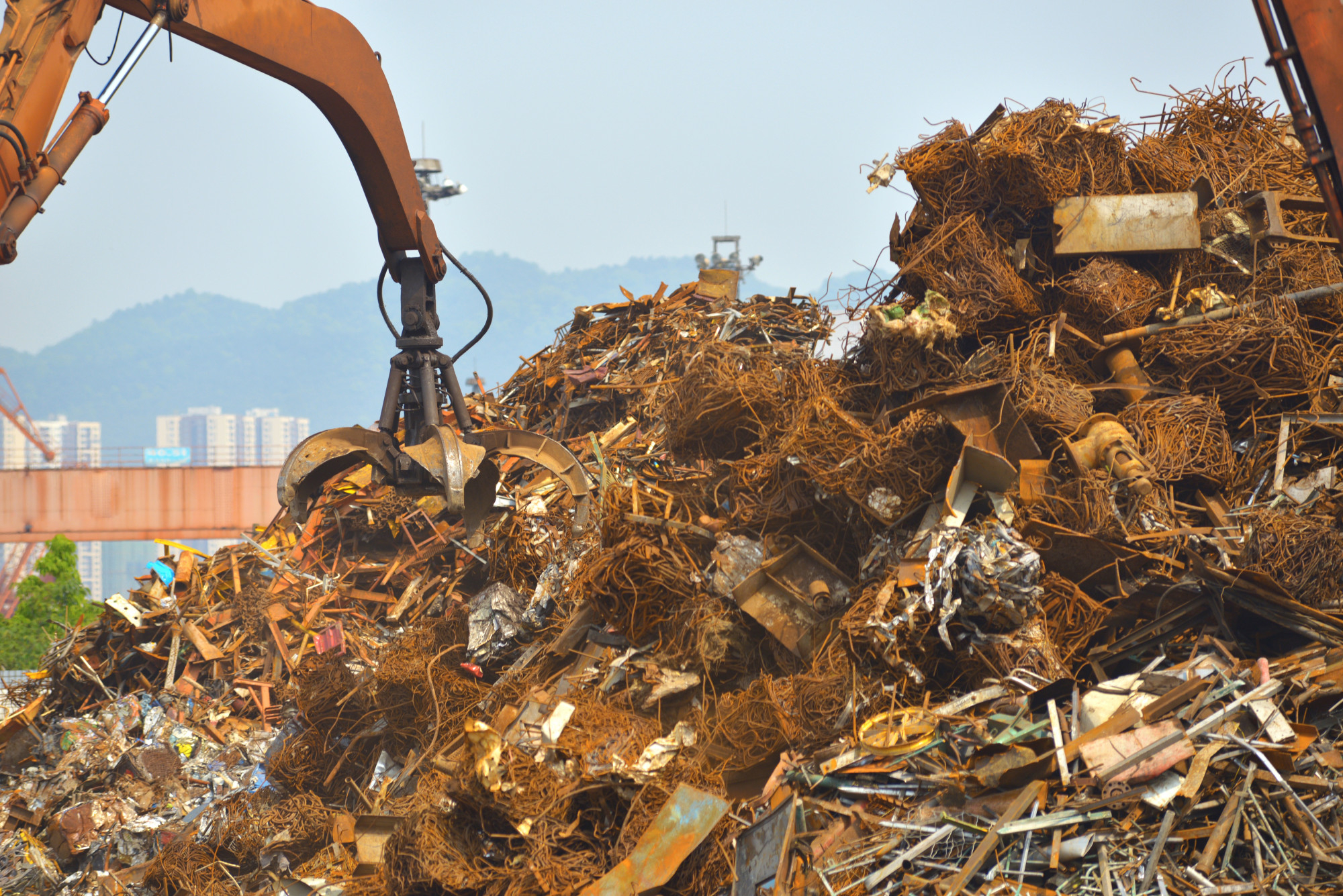
However, some elements, especially copper, cannot be removed during the steelmaking process. Elevated copper levels in steel can lead to a loss of ductility and resulting surface defects. Copper content is currently carefully managed through a combination of sorting and dilution.
Looking forward, the broader electrification of society will lead to a higher proportion of copper in recovered scrap, and an increase in scrap availability and a corresponding reduction in ore-based production will reduce the amount of virgin metal available for dilution. Improved scrap sorting and better separation techniques to reduce contamination by trace metals like copper will be important to ensure all of steel grades can be produced via the secondary route.
Applying circular economic principles to product design (designing for remanufacture and recycling) will make ferrous and valuable non-ferrous metals such as copper easier to separate and recycle.