Lithoz and ceramic 3D printing
Lithoz, a leading developer of industrial ceramic 3D printers, has already successfully accessed the potential offered by ceramic 3D printing for aerospace applications. Lithoz’s CeraFab S65 industrial printer with Lithography-based Ceramic Manufacturing (LCM) technology offers ultra precise 3D printing with exact repeatability in serial production.
One highly in-demand quality of Lithoz’s LCM technology is the ability to 3D print ceramic casting cores for aircraft turbine blades. As already mentioned, 3D printed ceramic casting cores are crucial for producing complex turbine blade cooling channels. The speed and volume at which Lithoz’s 3D printers can produce these parts drastically reduces development time, speeding up time-to-market.
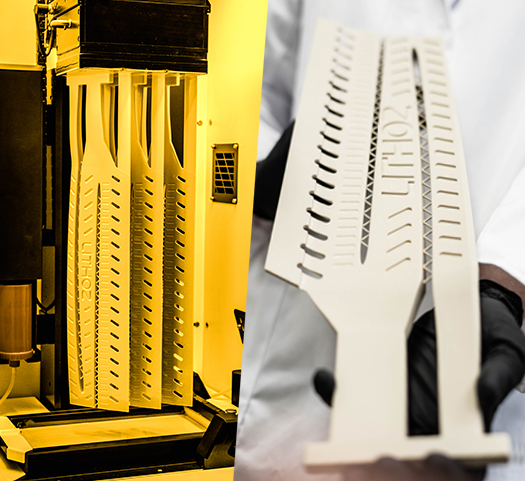
Ideal for manufacturing complex and precise ceramic parts, Lithoz’s CeraFab Multi 2M30 LCM 3D printer also offers multi-material capabilities. This 3D printer can combine different ceramics with metals or polymers, allowing for groundbreaking multi-functional parts with a combination of many desirable material properties in a single part. Lithoz’s new two-vat system allows these different materials mixed layer by layer or even flexibly graded in the same layer during the same print job.
For instance, this two-vat system allows for tailored porosity to be achieved. Lithoz’s multi-material LCM 3D printers can overcome the main problems of conventional manufacturing techniques for fabrication of porosity graded alumina, with desired microstructure and gradient architecture. This is ideal for R&D applications for ion thrusters.
Lithoz’s LCM process combines the desired aerospace properties with the otherwise unachievable flexibility of 3D-printed designs. This results in the production of fully dense parts with unmatched detail and precision.
As a result, parts can be 3D printed that are stronger and possess a longer lifespan than metal, resulting in less space debris and less downtime. What’s more, these ceramic components can also incorporate complex designs previously unthinkable when using conventional production methods.
Lithoz have also scaled up their technology to the level of industrial serial production. Therefore, in addition to the technical and material advantages offered by LCM, production can be ramped up to serial level for 3D printing high-quality parts at volume.
One perfect example of how LCM ceramic 3D printing will change the level of efficiency in aerospace applications are ceramic RF filters. Such filters are electronic circuits which play a crucial role in enhancing signal quality and minimizing interference in communication systems. Ceramic 3D printing with LCM technology allows for the necessary complex and precise shapes of these filters to be systematically produced in a miniaturized format. This shrinkage of the entire application allows for a significant weight reduction, the number one objective of aerospace engineers.