3D printing ceramics for aerospace applications
It is widely known that additive manufacturing can produce parts that are more durable and complex than anything currently possible through conventional manufacturing methods. Moreover, when manufacturing components for space and aviation applications, it is vital that the chosen material will withstand even the most extreme thermal conditions.
Therefore, 3D printing with ceramics offers the perfect combination for producing parts that are both highly complex and therefore more efficient, capable of performing in harsh and demanding environments.
Indeed, engineers are always searching for ways to increase efficiency, reduce consumption, limit waste, improve cooling, and achieve longer uptime. Combining the design freedom of 3D printing with the durability of ceramics offers the ideal solution for this.
One key benefit offered by this combination is the reduction of space debris. Thanks to their durability, ceramic parts can be used where even the toughest metals fail. Within an aerospace context, metals possess a shorter lifespan than ceramics, and will fail faster when exposed to extreme thermal conditions. These failed parts become space debris. Using ceramics reduces space debris as stressed parts show less wear under these extreme conditions.
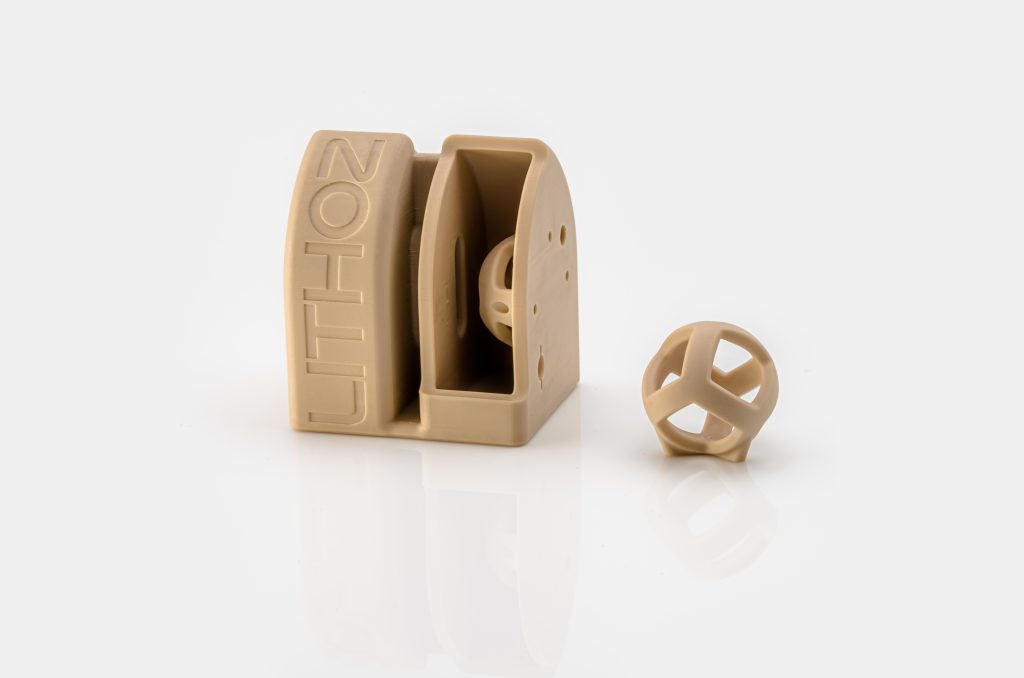
Additionally, 3D printing with ceramics allows for the production of highly precise and intricate parts. Within spacecraft, parts ranging from thrusters and sensors, to complex aviation casting cores with intricate channels, require an incredible high level of precision and accuracy.
Within aviation, stricter emission regulations require ever more complex cooling channels in turbine blades to achieve better efficiency by more refined cooling. The traditional investment casting method is not able to produce such fine structures. 3D printed ceramic casting cores allow for much better design freedom, higher part complexity and ultimately the desired improved cooling effect.