A variant of Horn’s Supermini precision tooling system has been introduced with new HP geometry, allowing higher infeed rates and other cutting parameters.
It also enables multi-functional use on a lathe across a range of operations including drilling, boring, face turning and skimming.
Holes from 3mm to 7mm in diameter may be drilled into solid material using Supermini HP tools without a chipbreaker. While the performance data cannot compete with normal drills, the system is a practical solution if the number of cutter locations in a machine is limited. With the single-edged version, various hole diameters can be produced with a single tool.
The Supermini HP offers the option of immediately boring an inner contour after drilling without having to change the tool. An accurate 90° shoulder can be achieved at the base of the hole and the wiper geometry produces excellent surface quality, even at high feed rates.
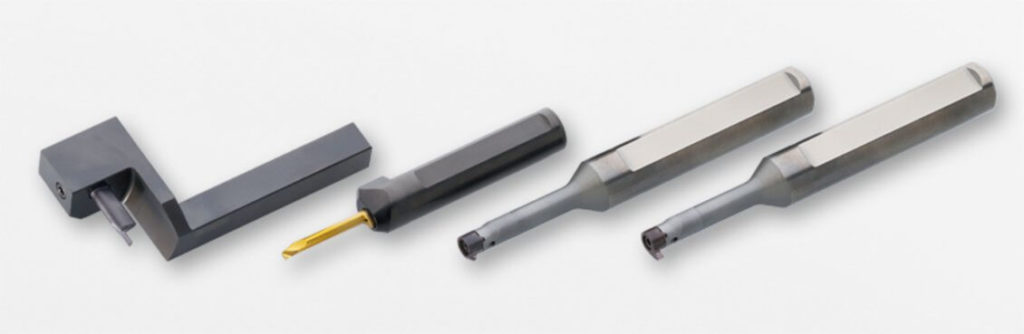
Source: Horn USA
Horn also provides tools with a chipbreaker, which are recommended for turning applications. The slightly twisted flute helps to remove chips efficiently from the machining zone, while an EG35 coating allows versatile machining of both standard and stainless steels.
In addition to the HP geometry, Horn has developed a new design of toolholder for the Supermini type 105, whereby clamping is achieved using a tensioning wedge on the face rather than on the circumference, as was previously the case. The tool is held in place with more force, which in turn makes the entire system more rigid.
Additionally, the new clamping design results in a higher level of repeatability when changing the tool and allows a more compact construction. Even when working with Swiss-type lathes, a user is able to change the tool without removing the holder.