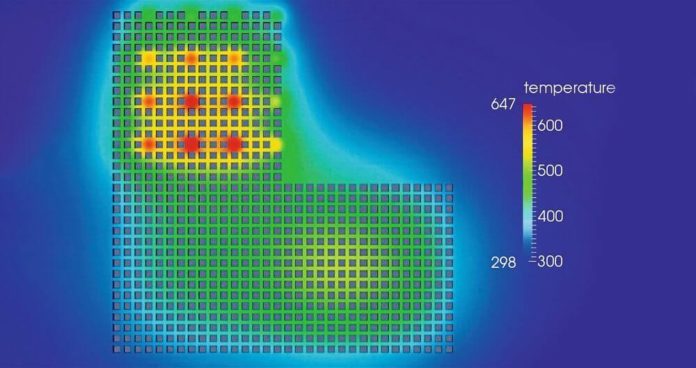
A new generation of ultrafast process technology is on the market. Higher average laser power and greater pulse energy promise higher throughput and efficiency.
The current challenge is to develop new beam guidance and process concepts to distribute the average outputs over the workpiece surface. It is process technology that currently poses the main limitation: Laser systems with high repetition rates require scanners with speeds of up to 1,000 m/s, while laser systems with high pulse energy require new beam-splitting and shaping concepts to distribute the energy. “It’s all about how we apply the power,” said Dr. Arnold Gillner.
Using DOE’s
One option for making better use of pulse energy is the multibeam concept, which involves splitting a laser beam into many beamlets. At the Fraunhofer Institute for Laser Technology ILT, a team has been working on this technology since 2012. Since then, the experts have learned how to use diffractive optical elements (DOEs) for the targeted application of over 200 beamlets in micro and nano-structuring. This allows them to obtain precise results in the sub-micrometre range.
For the DOE, the team uses a structured glass surface on which light waves are bent. The surface structure is etched into the glass with extreme precision using a wet chemical technique. As a result, the DOE’s static beam distribution is much more precise and resistant than dynamic beam-shaping approach based on liquid crystal modulators. For efficient material processing, the laser beam is transformed by a DOE into a beam matrix with many parallel beamlets. Using a scanner system and f-theta optics, the parallel beamlets are then focused on the workpiece and can be moved simultaneously over the workpiece along all possible paths.
In micro-drilling, the team from Fraunhofer ILT has achieved extraordinarily high precision. With their new multibeam system, the experts in Aachen are able to create precision holes with diameters of less than one micrometre. The spacing between holes can be reduced to a few micrometres. To increase throughput, they work with a DOE that generates over 200 beamlets.
This way, they have already managed to produce over 12,000 holes per second with an outlet diameter of under 1 µm.