Unisig‘s new range of USC-M deep drilling and milling centres provide mould makers seven powerful and versatile solutions for workpiece diameters and weights of up to 3,600mm and 30t respectively.
All machines combine several processes in one machine: deep-hole drilling and milling takes place on all four sides of a workpiece, reducing set-up time, while increasing accuracy. The machines also support high feed rates of modern indexable gun-drill tools.
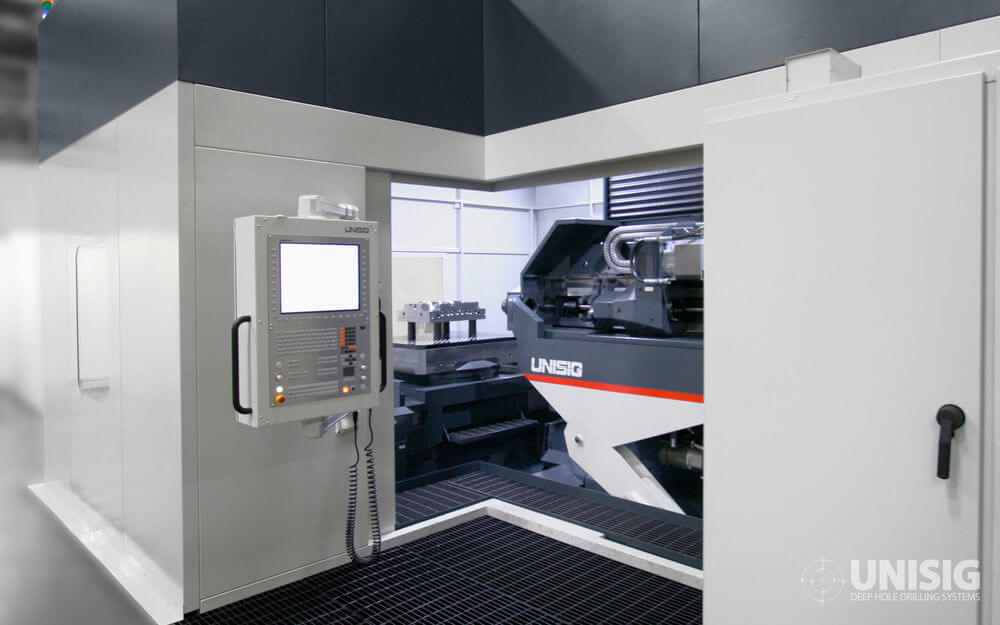
Apart from using gun-drill, deep-hole drilling tools, several models of the range support the more effective BTA deep-hole drilling tools for the high-performance drilling of waterline holes. Also, a CAT-50 quill enables all deep-hole drilling tasks and machining operations.
The machines are equipped with a 360° rotary work table and a programmable deep-drilling and machining spindle. These can be aligned using a pivot axis adjusted at 30° downwards and 15° upwards. The machines come with both Heidenhain’s TNC 640 CNC controller and motors, and drives are used. A complete cover with oil mist extraction rounds up the machine.
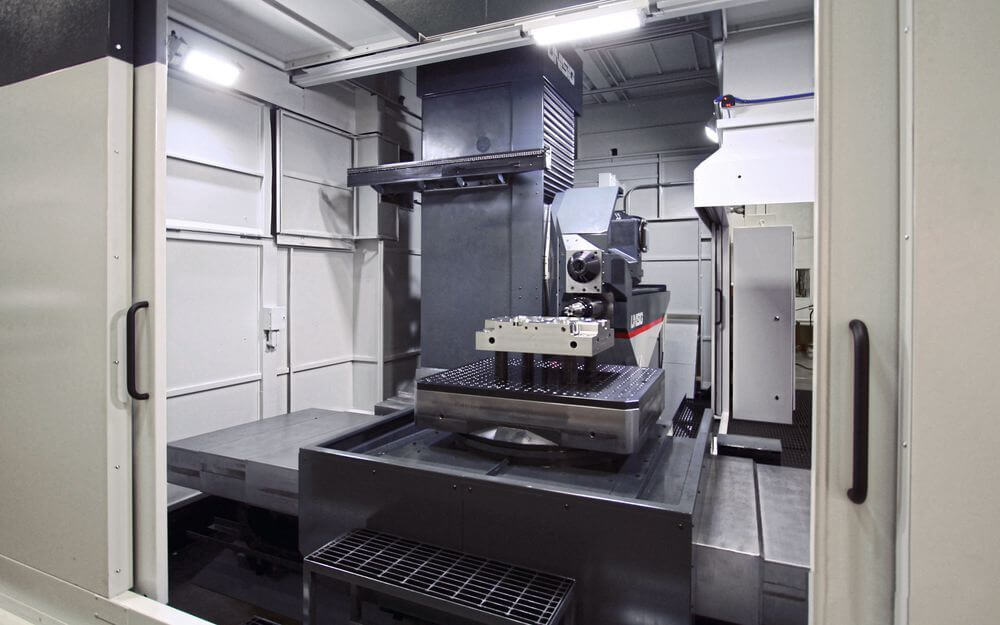
This USC-M series has been expanded to include 4-6 axis models: for deep-hole drilling with gun-drilling tools and milling, with a universal spindle and a quick switch between deep drilling and milling operations for small to medium-sized workpieces.
5-7 axis machines are available for gun drilling and more efficient BTA deep-hole drilling tools, each with a designated spindle to increase performance: 7-axis machining centres for dynamic motion control, powerful milling spindle with gear reduction and an optional pallet changer.
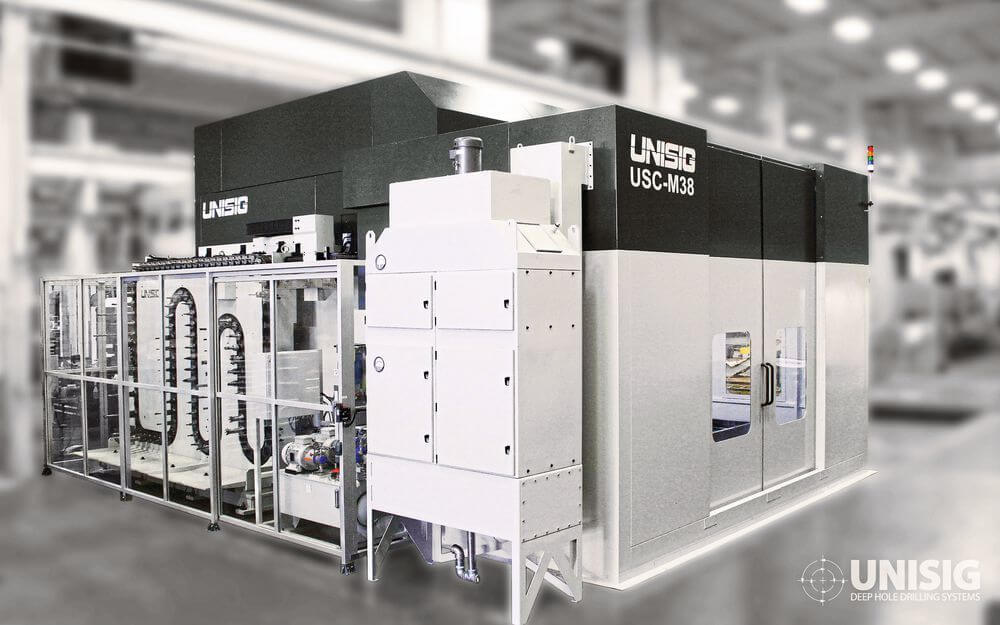
Source: unisig.com
The USC-M38 enables workpieces with lengths of up to 2,000mm to be conventionally machined and deep-drilled in one clamping. USC-M50 can handle up to 3,000-mm workpieces.