Medtech contract manufacturer Autocam Medical (Kentwood, Mich.) said that three new pieces of its manufacturing equipment have been installed in Western Michigan University’s (WMU) regional state-of-the-art advanced manufacturing partnership laboratory (AMP Lab).
The company is a partner in the AMP program, which focuses on encouraging and aiding the development of students pursuing careers in engineering and manufacturing. As part of an apprenticeship program, Autocam Medical sends workers to the university in Grand Rapids, Mich. to study computer numerical control (CNC) machining. Students who complete 728 hours of classroom instruction while maintaining a full work schedule receive their journeyman’s card in CNC machining and 27 college credits toward an associate’s degree.
Now students in the program will have access to some specialized equipment. The AMP lab equipment, a CNC 5 Axis Mill, a Swiss lathe, and a 3D metal printer, will provide engineering students and current engineers and designers with an opportunity to experience the high-tech devices needed to develop and test new products and prototypes.
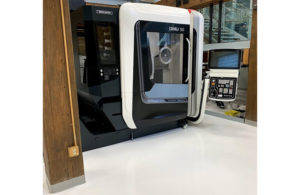
Source: Autocam Medical
The CNC 5 Axis Mill is used to make metal orthopedic devices such as ankle replacements, shoulder implants, hip sockets, and trauma plates for stabilizing broken bones. The Swiss lathe is designed to make long and slender round components, and the 3D metal printer can print ready-to-finish objects.
“We are primarily focused on the medical industry, so the machines are designed to make smaller parts,” said John Kennedy IV, general manager at Autocam Medical said in a news release.
Students will also be able to receive valuable input from industry experts at the lab. “Engineering students that have a concept that is a little bit more technical than what they have the ability to do on the Web, can come down here and say, ‘I have this great idea. Can you guys help me figure out how to make this?’ while they learn more about advanced machining,” Kennedy said.