Männer has developed a mould with an innovative cluster concept to ensure moulders can produce high-quality parts at a rate that meets high industry demand.
Disposable IVD articles that require high precision, high quality, and high production volume are now possible.
Pharmaceutical companies are currently extending their production capacity for manufacturing pipette tips in order to meet tremendous demand. Due to complex automation, investments can run into the millions — capital outlay that must be recouped through unit prices of only a few cents. This means moulds must achieve consistently high output volume and low scrap.
Männer has developed a mould concept for pipette tips which satisfies rigorous technical requirements while also emphasizing continuous availability, the company states. The concept is also compatible with existing systems on the market so customers can integrate the mold within existing production units.
The mould concept features multiple clusters, with each cluster having eight easily removable and replaceable cavities. Each cluster contains a nozzle head and its own electric supply for the independently heated nozzle tips, enabling mold maintenance directly on the machine. A cluster simply needs to be swapped out for production to resume. This approach avoids nearly all downtime during 24/7 operations.
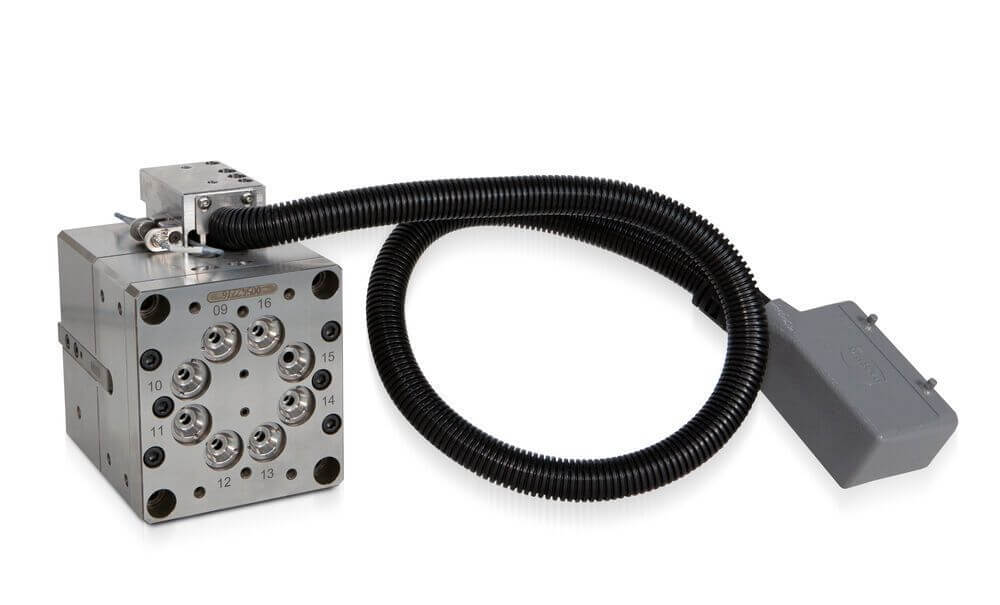
The company’s hot runner solution offers superior temperature control in 64-cavity moulds and ensures that a precise geometry of the pipette tip is achieved, including wall thicknesses from 0.25–0.30 mm and an opening of only 0.35 mm. Even the slightest core offset could result in filling imbalances and cause potentially inaccurate diagnostics results. The short-shot test revealed that all 64 cavities are optimally balanced.
The stable temperature balance and optimal design of melt channels solve several problems all at the same time. The thin core stays centered during injection, material dwell time is minimized, and the problem of “drooling” (i.e., the melt that keeps flowing into the cavity when the mould opens) commonly seen in open systems does not occur.
In order to expand its presence in the diagnostics sector, Männer is currently investing in additional production capacity. Through cooperation with injection moulding machines specialist Sumitomo Demag, automation specialist Micro-Automation, temperature control equipment specialist HB-Therm, and its affiliated Molding Solutions network companies, Gammaflux (temperature control systems) and Priamus (process control), Männer has a complete production unit in Bahlingen, Germany.
At the company’s headquarters, the pipette tip moulds can be optimized and given qualification testing concerning demoulding and automation. After qualification approval, the pipette tips are ready for use anywhere in the world.