Researchers from the Fraunhofer Institute of Production Technology (IPT) have developed a new additive manufacturing process specifically for the production of rotational power transmitters such as drive shafts.
Dubbed Express Wire Coil Cladding (EW2C), the method is intended as a more material- and cost-efficient alternative to the commonly used turning process, which is subtractive in nature.
Robin Day, Head of the Directed Energy Manufacturing department at the Fraunhofer IPT, explains: “Our idea was to change the shaft production more than just cosmetically. We wanted to develop a powerful process that would make producing complex shafts more cost-effective and resource-efficient.”
Express Wire Coil Cladding
EW2C is a laser-based 3D printing process that takes metal wire as feedstock. While most comparable to a process such as WAAM, there are some major differences that set EW2C apart from any other process out there. Rather than the wire being continuously fed in as and when needed, the new IPT process involves wrapping the wire (the added material) around an existing shaft (the substrate) in a helix-like spiral. A high power laser then welds the wire directly onto the shaft that it is wrapped around, forming cladding which can then be machined for a quality finish.
Since the wire is initially wrapped under tension, it doesn’t slip at all, reportedly improving the stability of the process by a factor of 10 when compared to Fraunhofer’s previously developed laser material deposition (LMD) process. Furthermore, the IPT team found the process to be capable of thick layer deposition, and were successful in applying wire thicknesses of 0.5 – 2 mm at a time.
To top things off, the new method is also able to match the cycling times of turning. In a test run, the team welded a 25 mm high, 1.2 mm thick spiral of Inconel 718 onto a steel shaft in under a minute. In this fashion, different combinations of metals can also be applied, such that the surface of the part can be intelligently functionalized and geometric shapes can be fabricated.
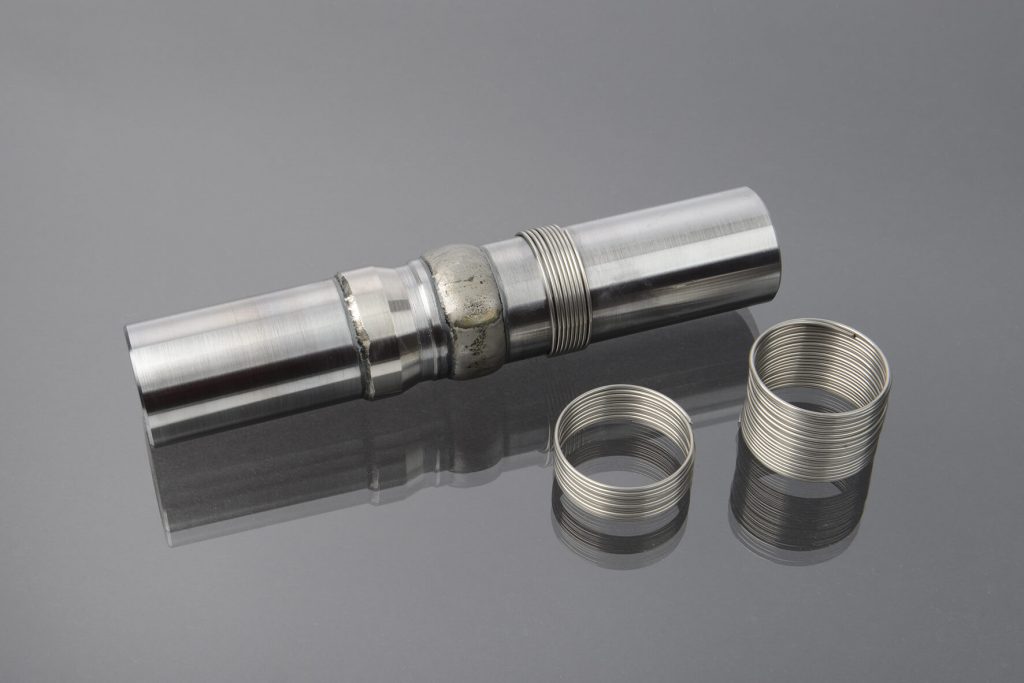
The next steps for EW2C
The IPT researchers have already filed a patent for their novel method, and are currently in the process of optimizing its stability while finding ways of automating it with various devices. The team plans to apply increasingly complex volume elements to the shafts via a combination of varying spiral lengths and advanced wired materials. Finally, the process’ suitability for both solid shafts and thin-walled hollow shafts (tubes) will also be tested.
Day adds: “To increase the process speed even further, we are experimenting with enlarging the focal spot geometry and thus irradiating and melting several spiral coils simultaneously. With concepts like EW2C it is possible to trigger greater innovations in industries that have developed evolutionary, but not revolutionary, for decades. Additive Manufacturing unlocks great potential, especially in the metal sector. We have only just begun to break new ground.”
In a similar project, a team from the Fraunhofer Institute for Ceramic Technologies and Systems (IKTS) has previously developed a Multi Material Jetting (MMJ) system capable of combining multiple materials into a single 3D printed part. The machine is based on inkjet technologies, and utilizes high-performance ceramics and metals to produce parts with novel properties.
Elsewhere, in Dresden, the Fraunhofer Institute for Manufacturing Technology and Advanced Materials (IFAM) recently launched a new additive manufacturing facility. The Fusion Factory, developed by industrial equipment supplier Xerion Berlin Laboratories, is intended as a miniaturized production line for the FFF printing of metallic and ceramic parts.