Making monitoring more accessible
When it comes to monitoring changing weather patterns in LEO, retarding potential analyzers (RPAs) are a vital piece of equipment. First deployed in a space mission in 1959, these multi-electrode instruments essentially detect the energy in the ions that float in the plasma molecules present in the Earth’s upper atmosphere. Also applied as in-orbit mass spectrometers, the versatile sensors are capable of measuring energy and analyzing chemicals to inform weather predictions.
RPAs themselves work by using a series of electrically-charged meshes with tiny holes to strip electrons and other particles away from ions, which in turn, create a current that can be measured and analyzed.
According to the MIT team, making such devices effective depends on ensuring their housing structure and meshes align, as well as their insularity and ability to withstand drastic temperature swings.
However, the scientists also point out that current plasma sensors tend to be made from silicon in cleanroom conditions, via a process that requires weeks of intricate fabrication. As such, RPAs can be very expensive, limiting their potential to be fitted to the CubeSats that are increasingly making LEO-based R&D more accessible. With this in mind, the MIT team have developed a means of 3D printing them from glass-ceramic instead, that could help advance in-situ ionospheric studies.
“If you want to innovate, you need to be able to fail and afford the risk. Additive manufacturing is a very different way to make space hardware,” explains Velásquez-García. “I can make space hardware and if it fails, it doesn’t matter because I can make a new version very quickly and inexpensively, and really iterate on the design. It is an ideal sandbox for researchers.”
“WHEN YOU MAKE THIS SENSOR IN THE CLEANROOM, YOU DON’T HAVE THE SAME DEGREE OF FREEDOM TO DEFINE MATERIALS AND STRUCTURES AND HOW THEY INTERACT TOGETHER. WHAT MADE THIS POSSIBLE IS THE LATEST DEVELOPMENTS IN ADDITIVE MANUFACTURING.”
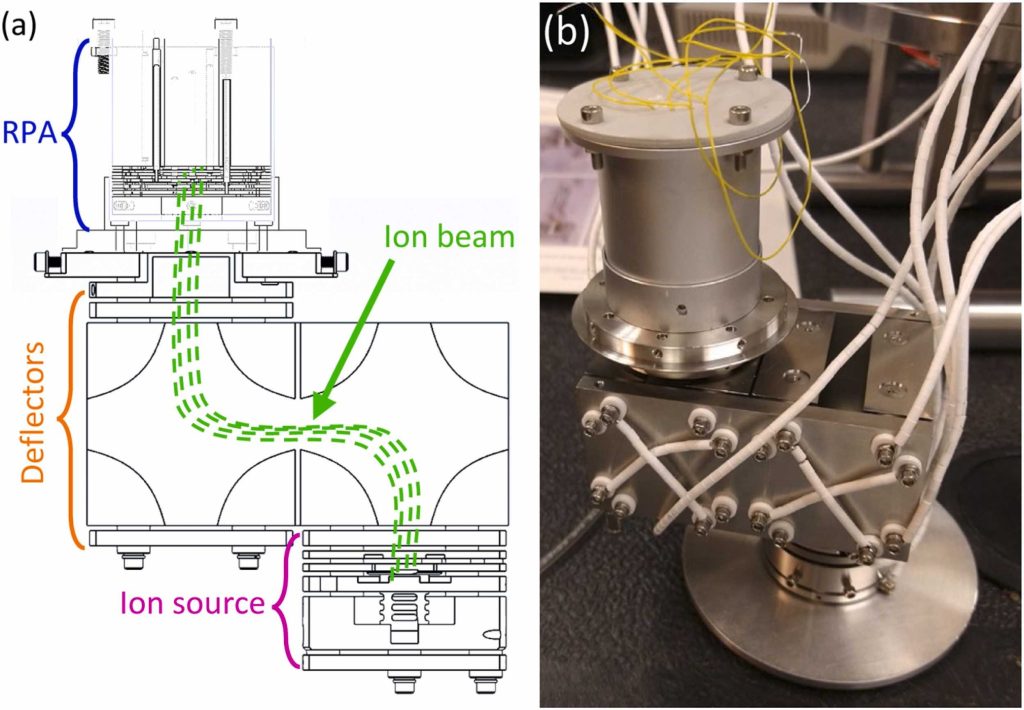