Australian heat transfer specialist Conflux Technology has partnered with German-based space rocket manufacturer Rocket Factory Augsburg (RFA) to embed their 3D printed Conflux heat exchanger technology into an orbital rocket.
The heat exchanger components are produced using Conflux Technology’s Monel K 500 metal alloy material, and printed using EOS M300-4 Direct Metal Laser Sintering (DMLS) technology. The gas duct heat exchanger is set to be developed, manufactured and put through a functional test later this year.
Part of the Australian Space Agency’s Moon to Mars Initiative, this project is funded by the Supply Chain Capability Improvement Grant Program which awarded Conflux $1 million AUD last year. This initiative and grant aids Australian run projects that could contribute to NASA’s ongoing mission to conduct human spaceflight to the Moon, and eventually Mars. Equally, the initiative also supports the Australian Space Agency’s long-term goal to grow the aerospace industry in the country.
“At conflux we are establishing ourselves as leaders in the development and commercialization of 3D printed thermal solutions and relevant materials for extreme applications,” commented Conflux Chief Commercial Officer Dan Woodford. “With support from the Australian Space Agency’s Moon to Mars Grant Supply Chain Capability Improvement grant, we are now applying it to the rapidly expanding space industry.”
When the funding was announced, Conflux CEO and Founder Michael Fuller said that “We are extremely excited to put our HXs into space! This grant will facilitate the technical development and commercial deployment of our heat exchangers in the most extreme environments…rocket engines.”
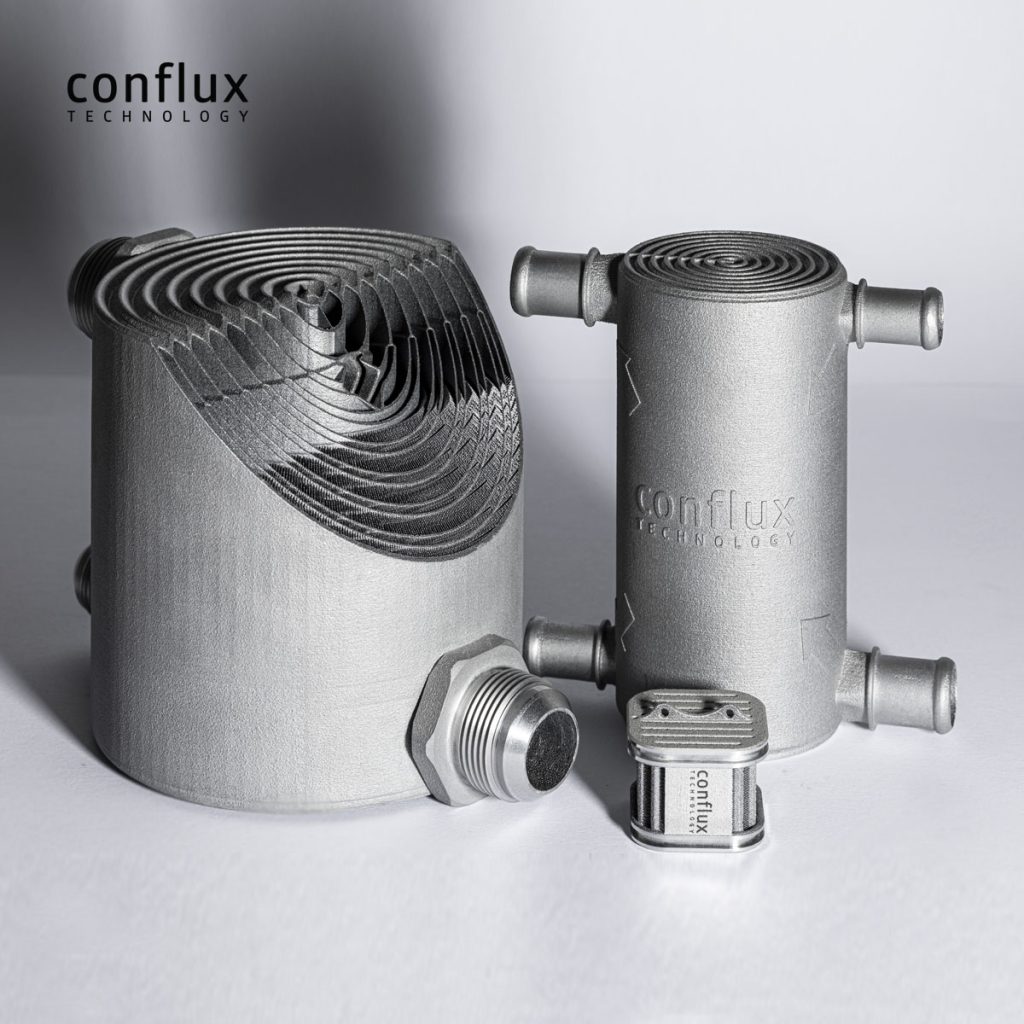
Conflux Monel K 500 and EOS M 300 technology
Conflux’s Monel K material, a nickel-copper alloy, is known for its high corrosion resistance, strength and durability, and sees extensive use in marine and chemical processing applications. Monel K is also notable for its resistance to stress corrosion cracking and pitting corrosion, a form of localized corrosion that causes the random creation of small holes in metal.
However, the K 500 variant has been further strengthened through age-hardening and precipitation hardening, offering improved strength and hardness. Thus, Monel K 500 possesses a high yield strength, tensile strength and improved corrosion and erosion resistance, making it ideal for high-stress aerospace applications and the production of heat exchanger parts.
To manufacture the heat exchanger components with Monel K 500, Conflux is leveraging their EOS M300 Direct Metal Laser Sintering (DMLS) machines, which they purchased last year. Offering a 50% increase in build volume over its predecessor, the M300 also offers strong reliability through improved layout, functionality, hardware and software.
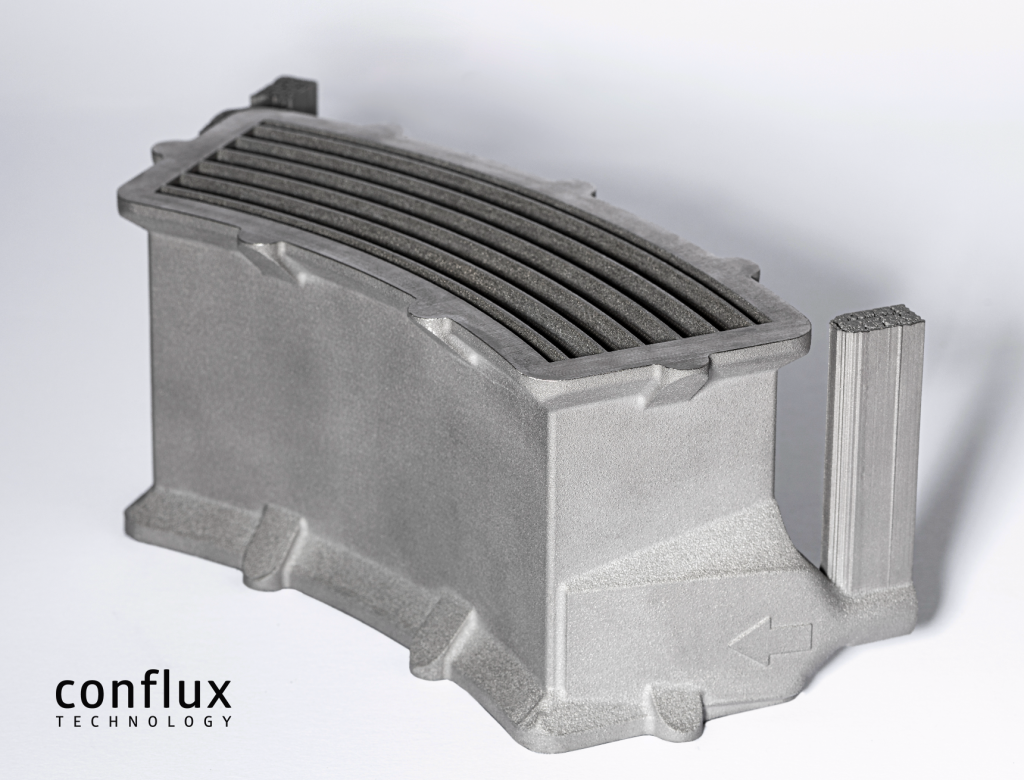
Additionally, the M300 incorporates 4x lasers which can operate simultaneously on any area of the powder bed, with each laser not being limited to a single working quadrant. This feature reduces build times, ultimately enabling a higher throughput for production. Moreover, the EOS technology also offers a gas-flow-optimized process chamber with the EOSYSTEM SmartCal calibration tool, ensuring high build quality and repeatability.