A team of scientists from the University of Sydney and the Children’s Medical Research Institute (CMRI) at Westmead have leveraged 3D photolithographic printing to fabricate functional human tissues that accurately mimic an organ’s architecture.
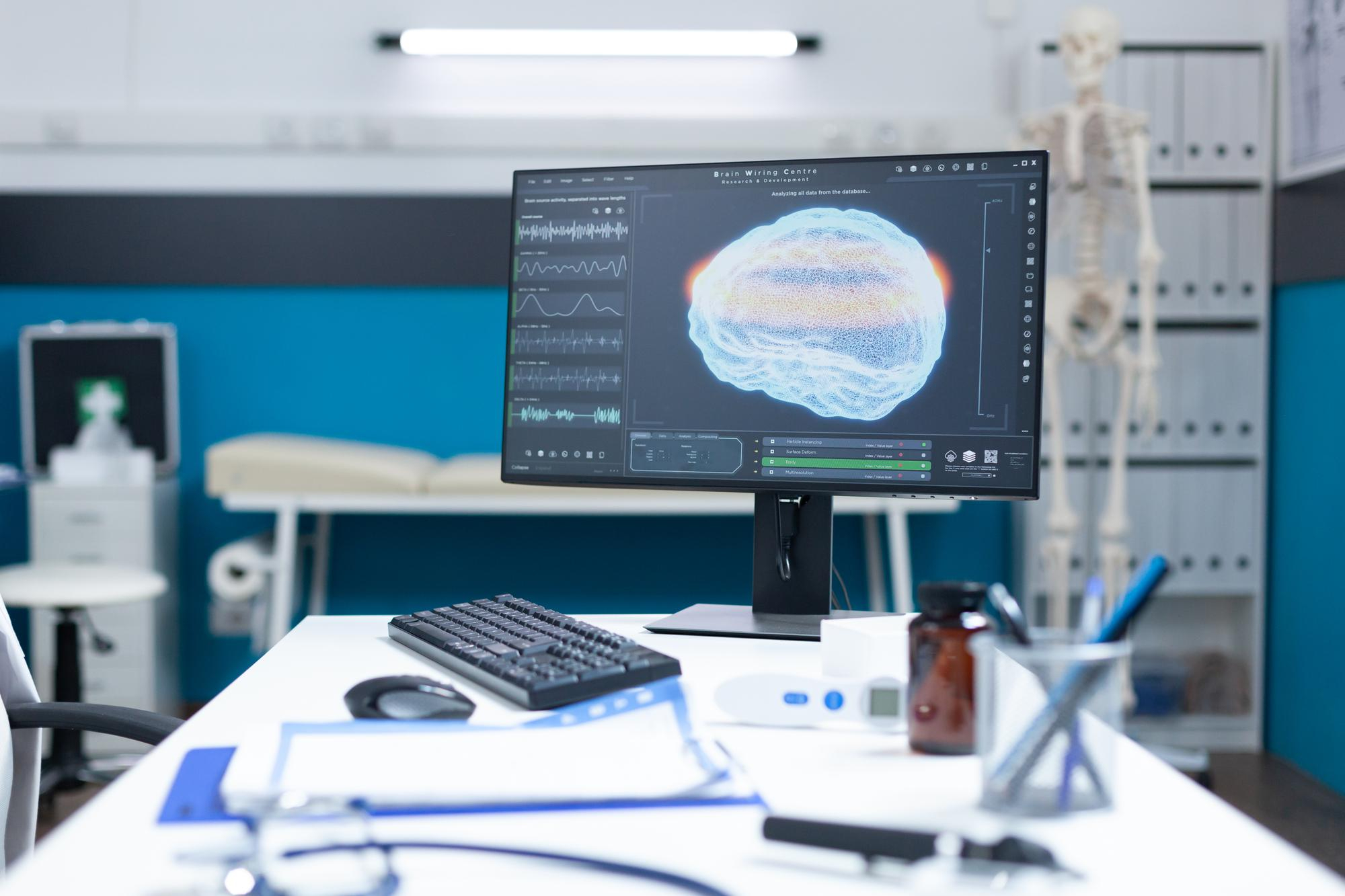
The researchers utilized bioengineering and cell culture techniques to instruct stem cells derived from blood cells and skin cells to become specialized. These specialized cells can then form organ-like structures.
This project was led by Professor Hala Zreiqat and Dr. Peter Newman from the University of Sydney’s Biomedical Engineering, and Professor Patrick Tam who heads the CMRI’s Embryology Research Unit. The team’s research paper, titled ‘Programming of Multicellular Patterning with Mechano-Chemically Microstructured Cell Niches’, has been published in Advanced Science.
Looking to the future, the research team will now focus on developing their technique to advance the regenerative medicine field, and pursue new treatments for a range of diseases.
“Our new method serves as an instruction manual for cells, allowing them to create tissues that are better organized and more closely resemble their natural counterparts. This is an important step towards being able to 3D print working tissue and organs,” commented Professor Hala Zreiqat.
AN “INSTRUCTION MANUAL FOR CELLS”
Cells require detailed instructions in the form of strategically positioned proteins and mechanical triggers to build tissues. According to Dr. Newman, without these specific instructions, the cells are likely to group together in unpredictable and imprecise ways.
Through this research, the scientists leveraged a novel 3D photolithographic printing technique to generate microscopic mechanical and chemical signals that guide cells into accurate and organized organ-like structures.
This technique was employed to successfully create a bone-fat assembly that resembles bone structure. An assembly of tissues that resemble processes during early mammalian development was also fabricated using this method.
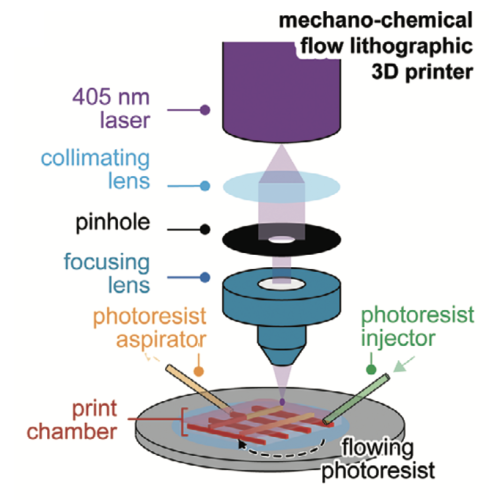
“In the past, stem cells were grown to generate many cell types, but we could not control how they differentiate and assemble in 3D,” commented Professor Tam. “With this bioengineering technology, we can now direct the stem cells to form specific cell types and organize these cells properly in time and space, thereby recapitulating the real-life development of the organ.”
POTENTIAL MEDICAL APPLICATIONS
It is hoped that this research will help to advance understanding of how organs develop and function, and how genetic mutations and developmental errors influence organ diseases.
Moreover, this study is said to offer potential for the development of cell and gene therapy. Indeed, the ability to produce desired cell types could facilitate the production of clinically relevant stem cells for therapeutic uses.
“This method has immense practical implications. For instance, in regenerative medicine, where there is a pressing need for organ transplants, further research using this approach may facilitate the growth of functional tissues in the lab,” explained Professor Hala Zreiqat.
Dr. Peter Newman added that “this technology could revolutionize how we study and understand diseases. By creating accurate models of diseased tissues, we can observe disease progression and treatment responses in a controlled environment.”
The researchers are especially hopeful that their findings can help to treat vision loss caused by macular degeneration and inherited diseases, resulting in the loss of retinal photoreceptor cells.
“If we can generate a patch of cells by bioengineering and see how the whole system functions, then we can investigate therapies that use functional cells to replace cells in the eye that were lost because of disease,” stated Professor Tam.
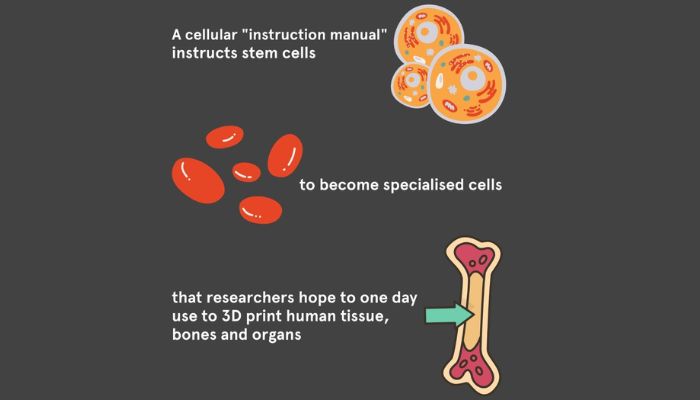
“It would have a great impact if we can deliver healthy cells into the eye. Regardless of whether the macula (the area of the retina responsible for central vision) had been lost due to inherited disease or because of trauma, the treatment would be the same.”
3D PRINTING ORGANS
Despite the promising findings of this study, the 3D bioprinting of viable, transplantable organs is still some way from becoming reality. However, a number of companies are making progress towards this long-term goal.
Last year it was announced that researchers from the Stevens Institute of Technology in New Jersey had employed computational modeling techniques to advance microfluidics-based 3D bioprinting, with the hope that this could enable the 3D printing of entire human organs.
“The scale is very important, because it affects the biology of the organ. We’re operating at the scale of human cells, and that lets us print structures that mimic the biological features we’re trying to replicate,” explained Robert Chang, the associate professor at Stevens’ Schaefer School of Engineering & Science
Elsewhere, a research team from Utrecht University has already succeeded in fabricating working livers using ultrafast volumetric 3D bioprinting.
The team successfully fabricated functional liver units of more than 1 cm³ in less than 20 seconds by 3D printing organoids, miniaturized units of around 1 mm made from stem cells that copy aspects of their tissue of reference. These liver units were able to successfully perform key toxin elimination processes, mimicking those performed by natural human livers.