Over the last three years, the international consortium made up of nine partners has succeeded in developing more resource-efficient production processes for the aviation industry.
CENIT played a critical role by providing the upgraded CATIA V5 CAD system that includes the relevant interfaces. The system can now map the 3D printing process of components completely in a single software program – from design to post-processing.
Thanks to the bionic support structures for the 3D-printing parts on the basis of unit cells recently developed by Fraunhofer Research Institution for Additive Manufacturing Technologies IAPT, software users can save material, time and thus costs in the future – with improved quality results. The research findings from “Bionic Aircraft” serve as the basis for cross-industry solutions in the field of additive production. Initial software training has already begun.
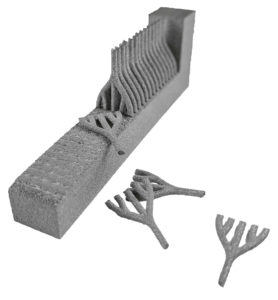
Source: Cenit
“From the start, 3D printing and bionic design played a fundamental role in the research project funded by the EU Commission. Ultimately, we had an ambitious goal, which was to reduce the weight of aircraft components and in doing so to ultimately reduce fuel consumption,” explains project coordinator Dr. Philipp Imgrund from Fraunhofer IAPT located in Hamburg.
With the interface from the CAD system CATIA V5 has for the 3D printer, components can now be printed from the CAD software directly. “Decisive in connection with this is that all process steps, including post-processing, can be mapped in CATIA V5,” says Jochen Michael, Senior Consultant at CENIT and adds:
“There is no need to exit the development environment and no data needs to be converted, which saves time and increases quality.”
The research work by Fraunhofer IAPT was inspired by nature. Whether butterfly wings or tree crown, each grid and branching structure inspired the project team to develop support structures for 3D parts using less material and at lower costs, with the added benefit that they are easier to remove. Support structures provide the needed underpinning to additive manufactured components at certain areas and must be removed after the 3D print either manually or by milling.
In addition to the latest development, the Fraunhofer IAPT team has validated existing support structures and assigned them to certain application scenarios. As a result, they can be automatically selected during the 3D printing process in the future.
Final milestone: the unit cell
In particular, the focus of the project partners over the past few months has been to iron out the fine details of the 3D printing process chain. With the resulting toolset, the support structures are now implicitly created. This means that in CATIA V5 a volume is created instead of the individual geometries. And the volume is attached to an attribute in the form of a color.
The volume is only filled with the geometry of unit cells in one of the following steps. “The unit cells make it possible to freely develop the support geometry, without affecting the performance of the CAD system. What is possible now, for example, are graded support structures in various layers that can differ in their structure,” explains Jochen Michael the innovation.
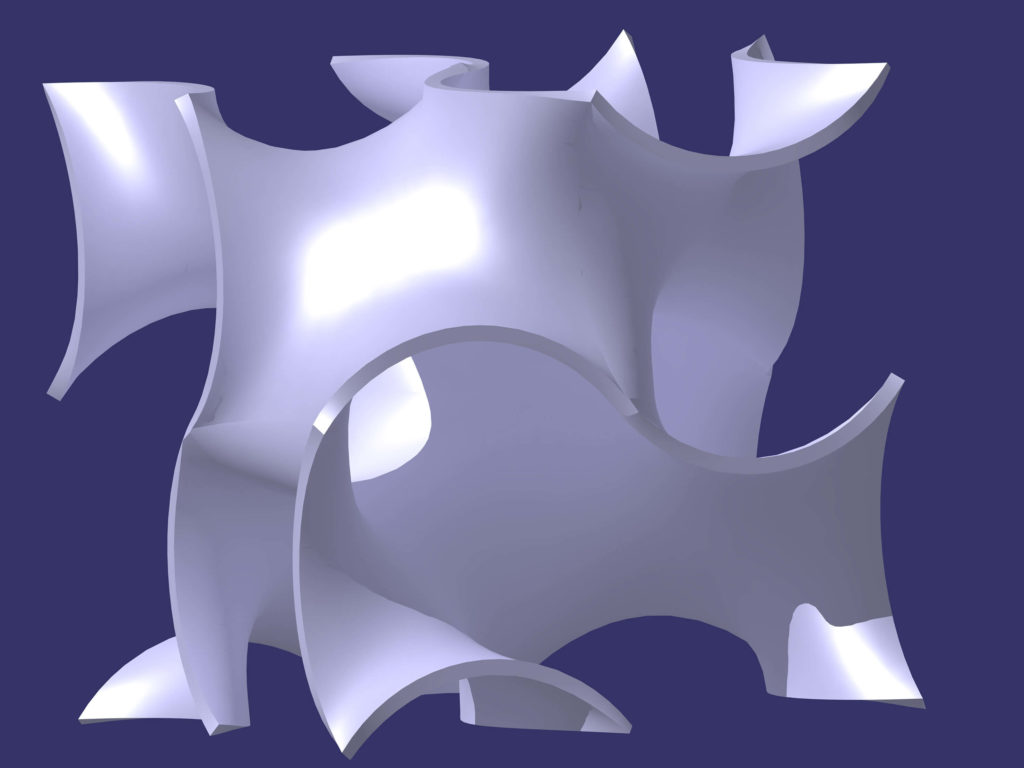
Source: Catia
A unit cell can be imagined as a cube of any size in which a geometry is generated. Any number of individual unit cells can be defined. These unit cells are divided into layers. The color (attribute) is linked with the corresponding unit cell in the configuration file. The advantage: The unit cells are only created once and can be re-used as many times as you want. The slice data are stored in a neutral XML format. Then, in a last step, the post processor developed by CENIT is applied. It generates the specific data for the machine. It generates the paths that the laser passes through during the exposure process and fills the areas with prefabricated unit cells. “The actual final geometry is not created until this point,” explains Dr. Imgrund.
“Bionic Aircraft”: more resource efficiency in the aviation industry
Since September 2016 to August 2019, the objective of the “Bionic Aircraft” research project funded by the European Commission has been to increase resource efficiency in the aviation industry. Nine international consortium partners from industry, research and development, among them also the IT specialist CENIT and the Fraunhofer Research Institution for Additive Manufacturing Technologies IAPT, are collaborating to come up with new methods and concepts. The focus was on additive production and bionic design.