At this year’s EMO Hannover visitors got to experience the latest machine tools, controls, automation technology and industry 4.0 solution from Okuma.
Innovative robot arm
A clear highlight of the Okuma booth was the revolutionary ARMROID technology. ARMROID is an articulated robot arm directly integrated into the machining area. The arm can autonomously switch its end effector for carrying out various tasks. One end effector is a workpiece hand that allows for easy automation by loading and unloading the machine tool.
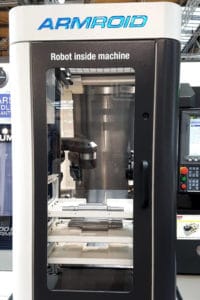
Source: Okuma
The second end effector acts like a follow rest and prevents chatter during turning operations by supporting the workpiece. With the third end effector, ARMROID is able to blast the cutting zone with coolant or air to break the chips safely. It can also be used for cleaning the machining area. When the arm is not in use, it is stored compactly, which facilitates operating the machine tool manually without obstructions.
Making automation easy and accessible
Together with ARMROID, Okuma also introduced STANDROID. STANDROID is an articulated robot arm integrated into a cell. As the cell can be placed next to machine tools, requiring only a connection to the network and to electricity, installing STANDROID is far easier than conventional robots.
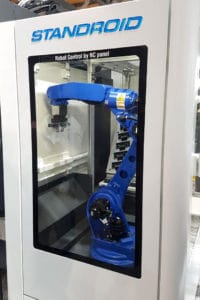
Source: Okuma
In addition, both ARMROID and STANDROID can be operated like a machine tool, making special trainings for staff unnecessary. Operators only need to define the start and end points of the robot’s motion. The control then calculates the best routes of the robot arm, and the Collision Avoidance System assures safe operations. For around-the-clock automation, Dutch Okuma partner BMO Automation showcased an automation setup at the booth consisting of product drawer modules, a robot and an Okuma machine tool.